Manual to home - Mill-Assist
![]() |
The robot has to be moved manually to the home position. This document describes the procedure. |
1. Use following tools
|
|
2. Procedure
2.1. Put the Robot in manual mode
Put the three-position switch on the Robot Controller to T1-Mode.
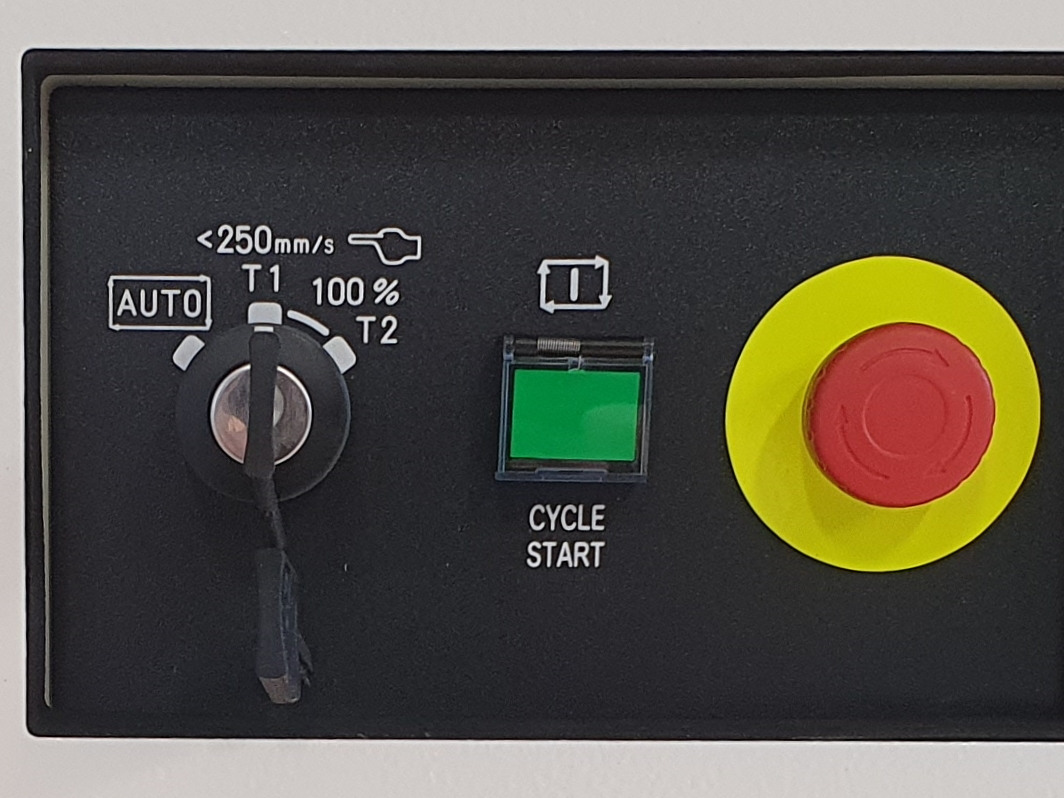
Put the two-position switch on the Teach Pendant to ON-Mode.
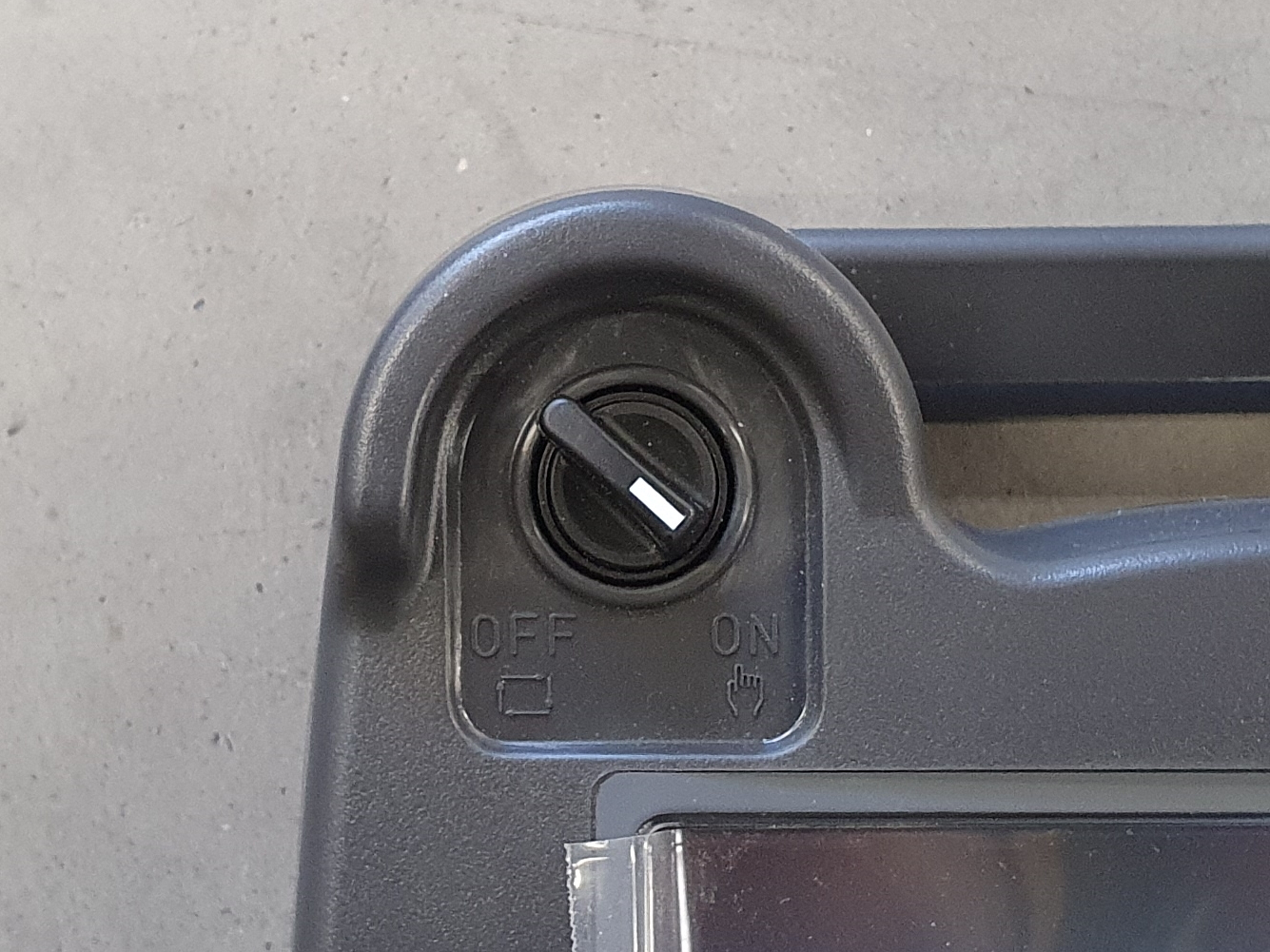
2.2. Abort all the running programs
RoboJob communication programs are still running on the robot.
Abort the running programs by pressing SHIFT + USER KEY 1. The USER KEY 1 is the first key underneath ENTER, sometimes also referred to as Unmarked key 1, Tool 1 or Unnamed 1. On newer versions of the Teach Pendant this key is a blank white key. On older versions of the Teach Pendant this button is the blue WELD ENBL button.
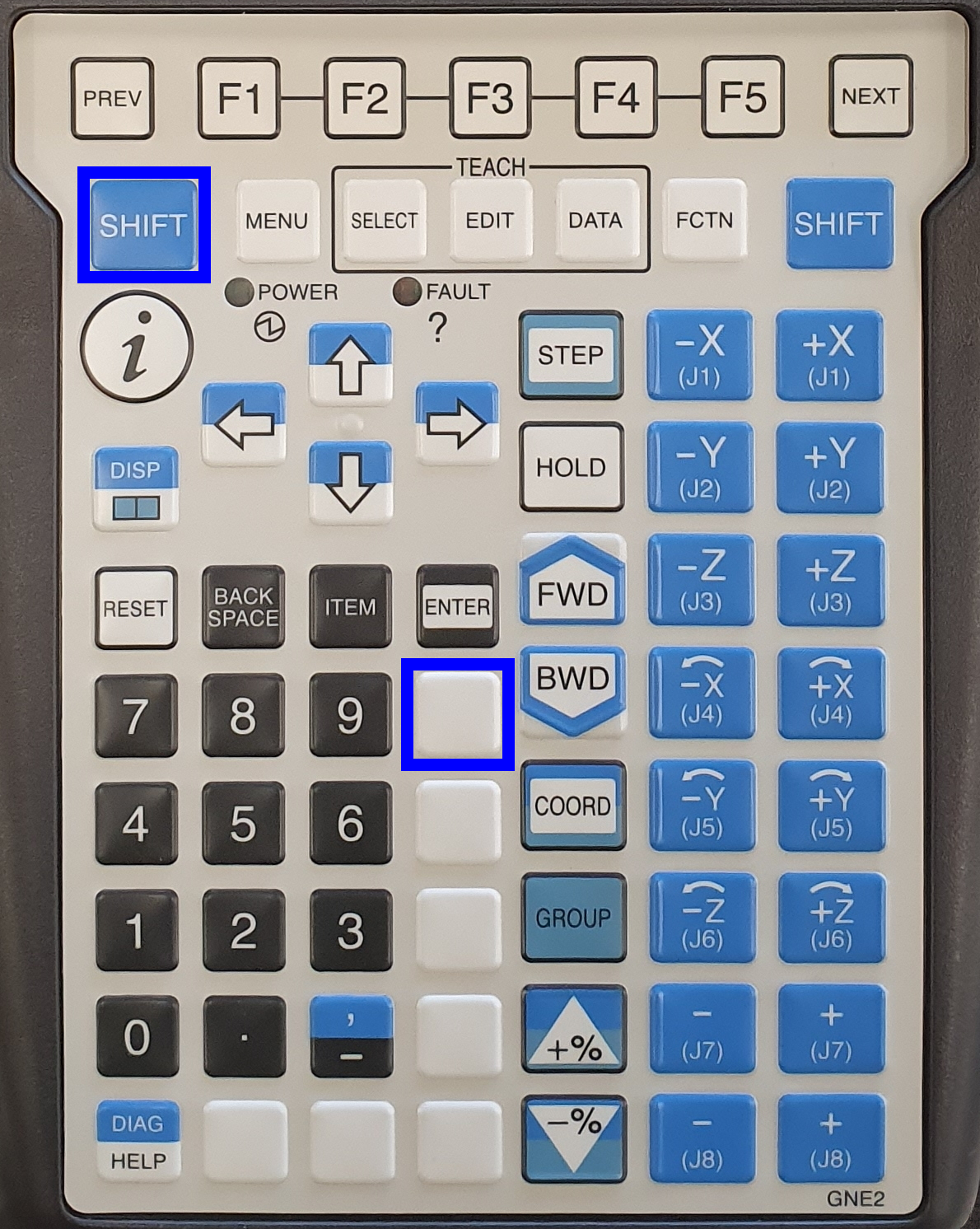
Verify that the software is stopped. The indicators Busy and Run on the top left of the screen should be yellow.
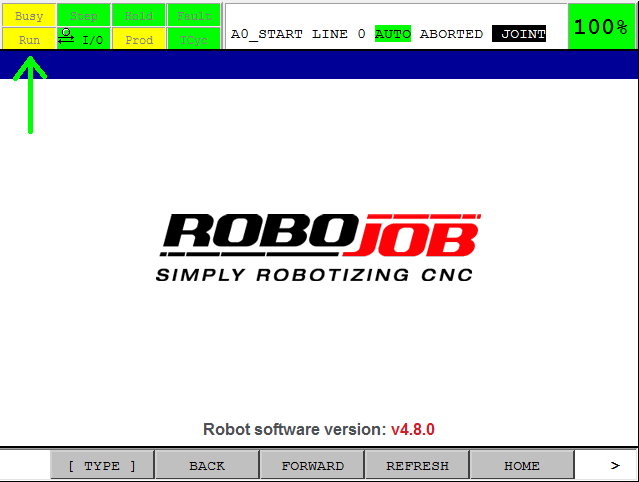
2.3. Reset all Faults and move the robot manual nearby his Home Position
To move the robot in a safe way, one deadman switch on the back of the Teach Pendant must be in the safe middle position.
Both deadman switches have 3 positions:
-
Not pressed
-
Safe middle position
-
Fully pressedTry if you can feel the three positions. To be able to reset the error and move the robot, only one of the two deadman switches has to be in the safe middle position. So don’t push too hard or too soft!
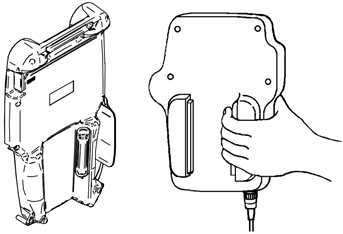
Press SHIFT + RESET to clear all faults. Fault indicator will change to green.
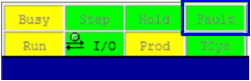
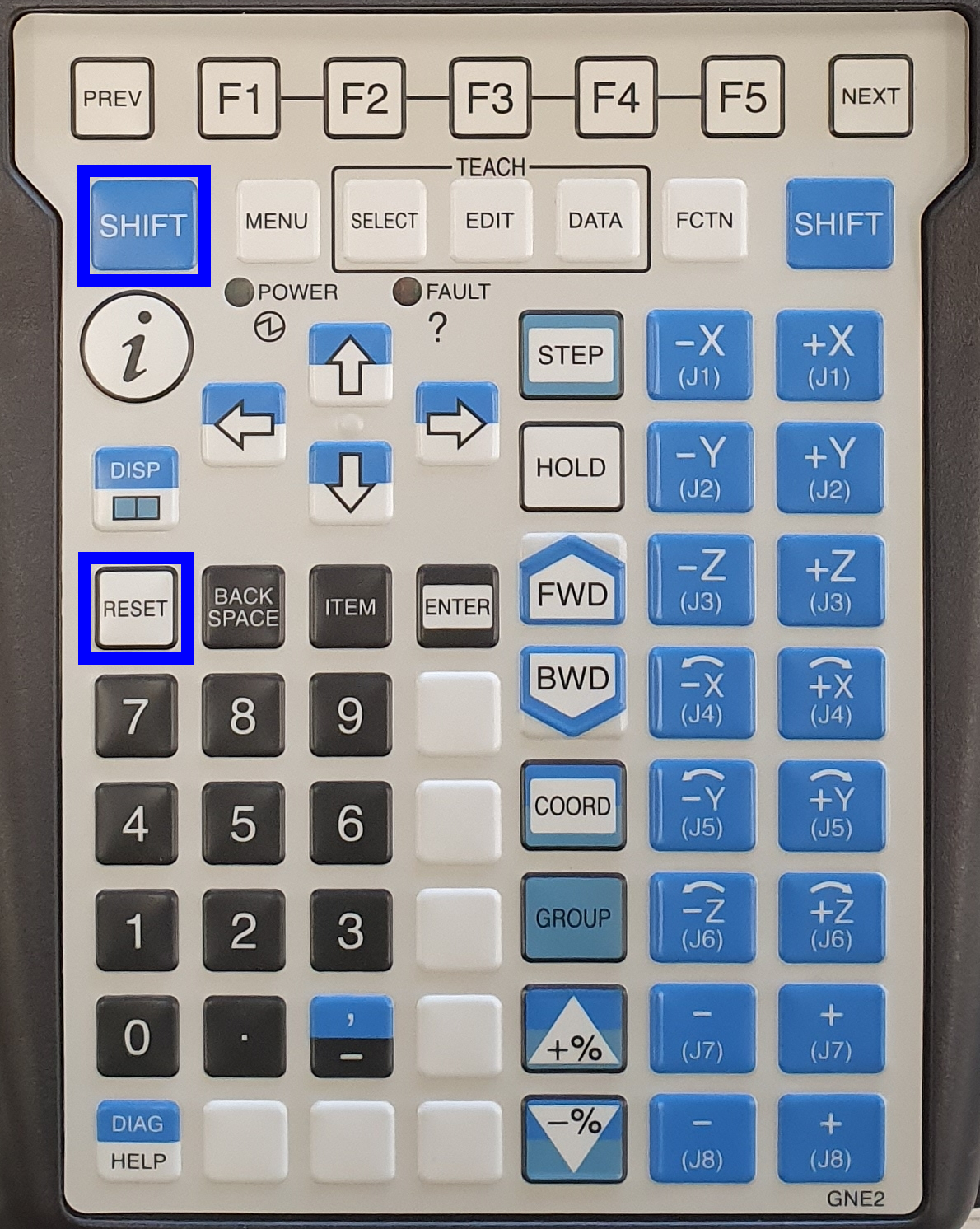
Now you are able to move the robot.
![]() |
Note |
Watch that the robot doesn’t hit anything during the movement. Watch out for other people, surrounding machines, other objects and the robot itself. Make sure the dress out cables around the robot don’t get damaged.
Press COORD to change the way of moving. Keep pressing until JOINT is selected. The JOINT movement mode is the easiest to work with. You move the Joints from the robot one by one.
|
|
Press SHIFT + ±J1-8 to move the robot close to its home position.
|
|
Press SHIFT + +% or -% to adjust the speed.
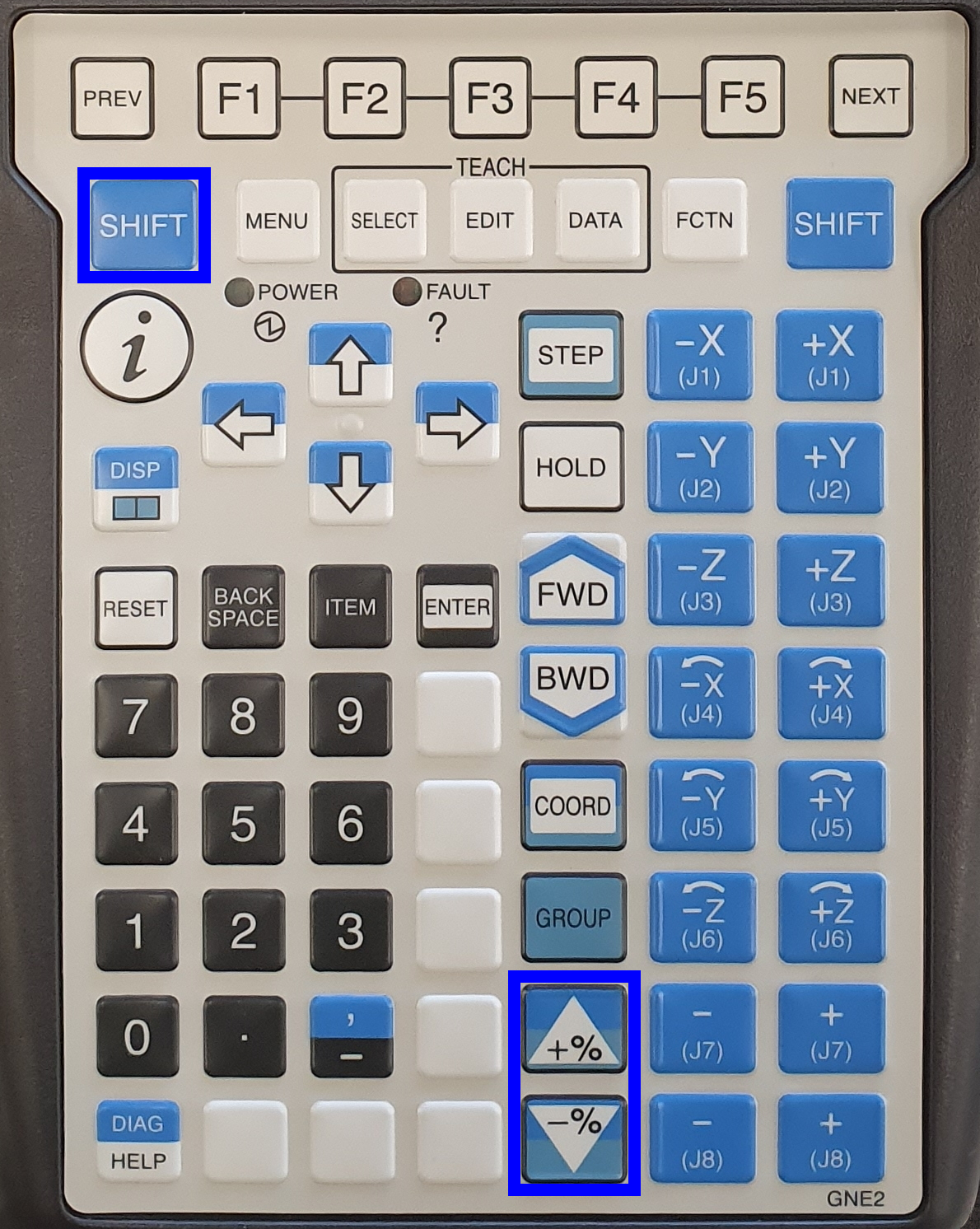
2.4. Select the program A5_MANUALTOHOME and execute this program
Press SELECT to open the program selection. Use UP and DOWN to select A5_MANUALTOHOME. Hold SHIFT to scroll faster.
When A5_MANUALTOHOME is selected press ENTER to open the program.
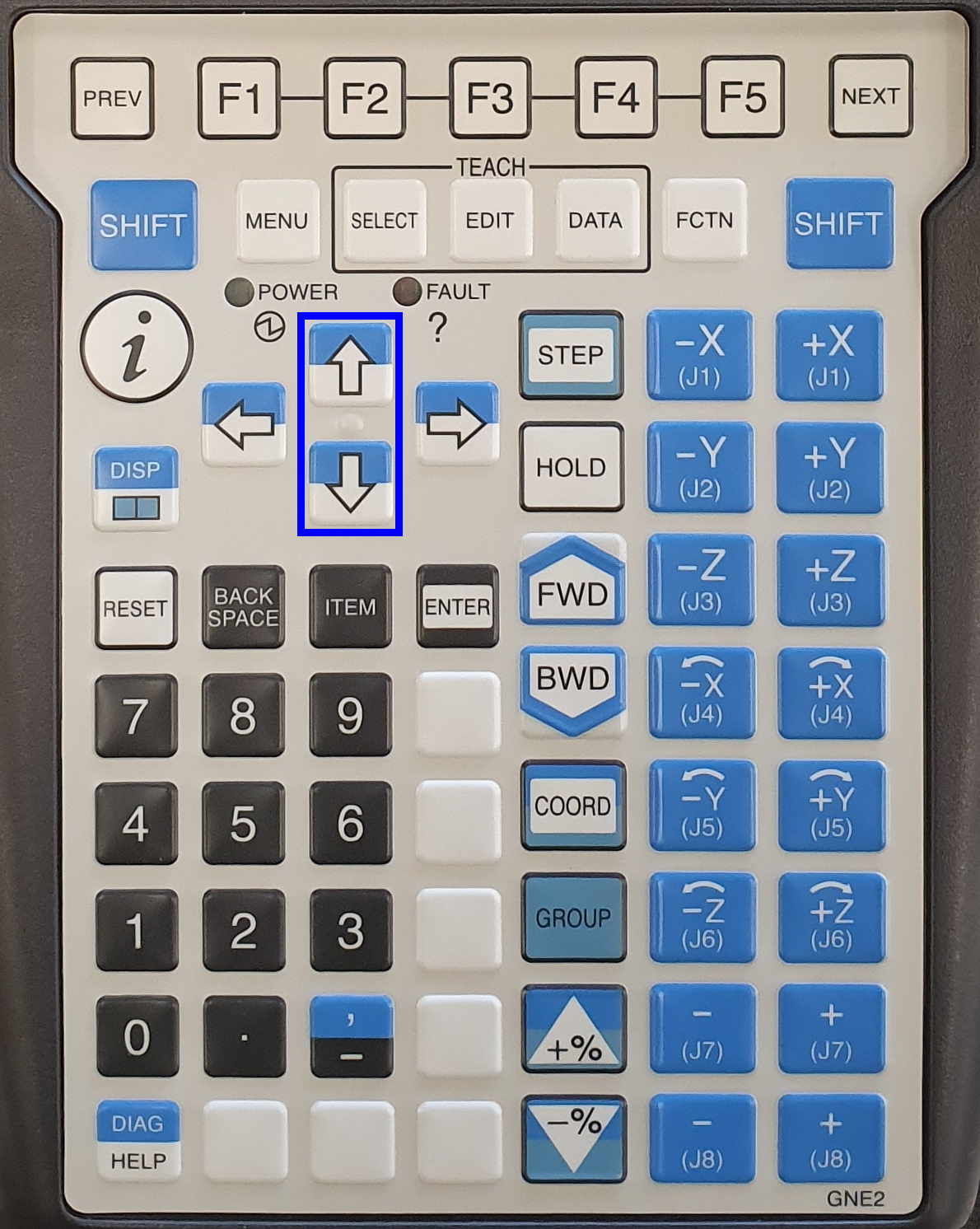
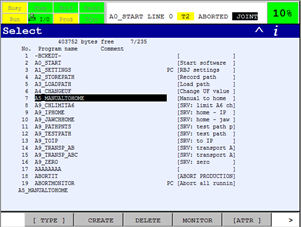
Press SHIFT + FWD to execute the program. The robot will move to the exact Home position. Release SHIFT or the deadman switch to stop the movement if needed.
The indicators Busy and Run will become green during the movement. Hold SHIFT and one deadman switch until the robot reaches the home position.
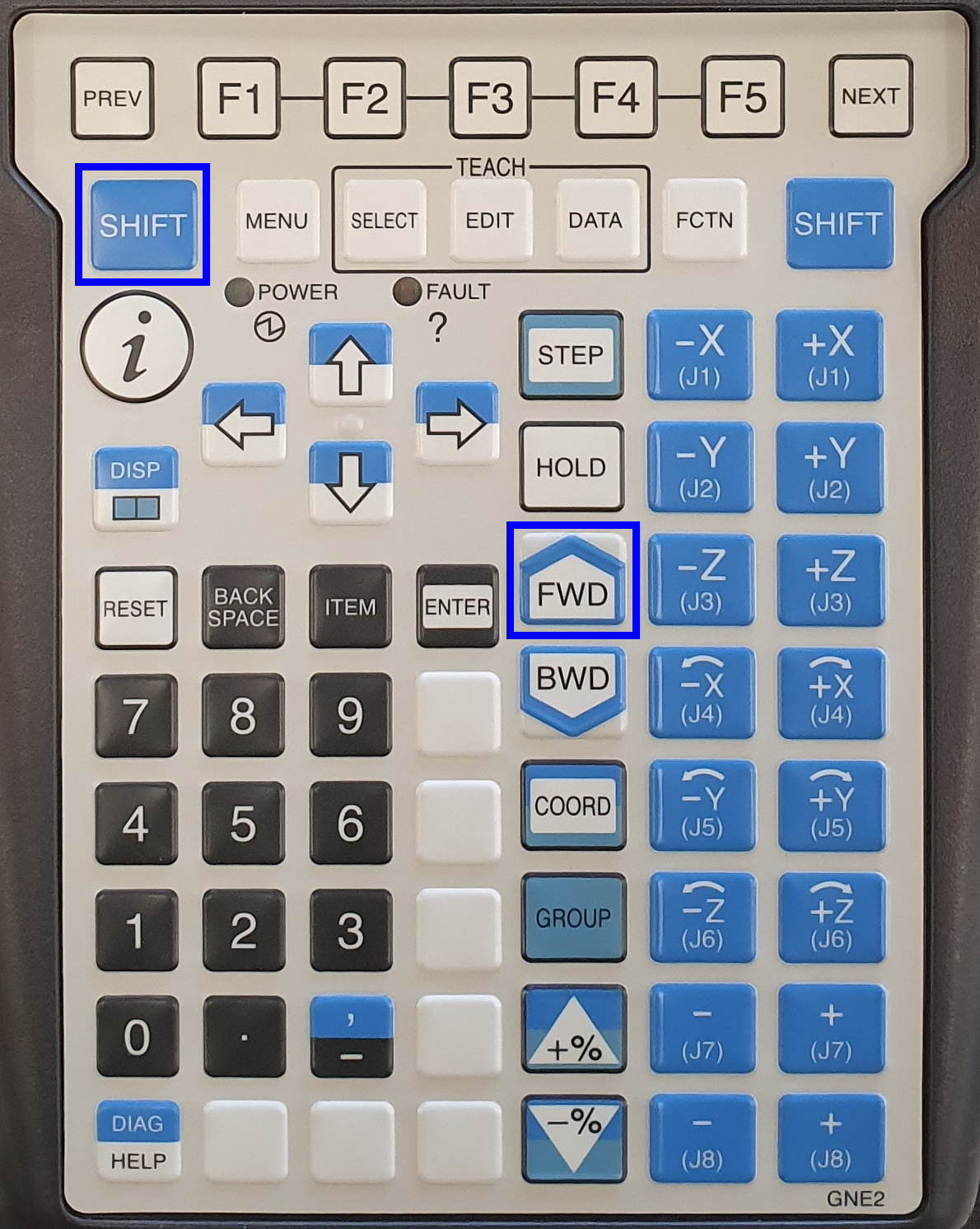
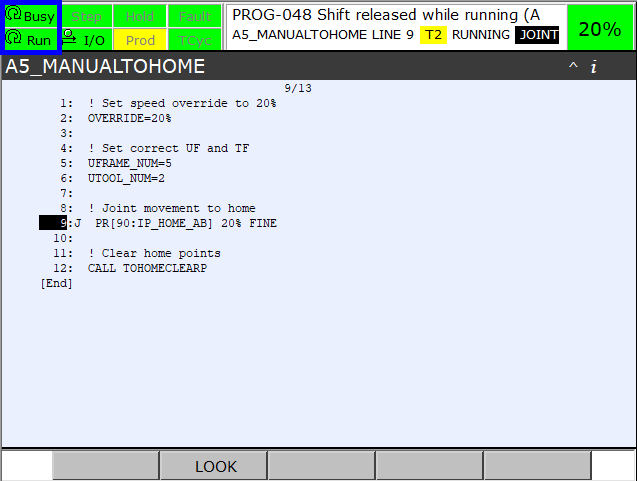
![]() |
Note |
Watch that the robot doesn’t hit anything during the movement. Watch out for other people, surrounding machines, other objects and the robot itself. Make sure the dress out cables around the robot don’t get damaged.
When the robot has reached the home position the indicators Busy and Run will become yellow again and the first line of the program will be selected.
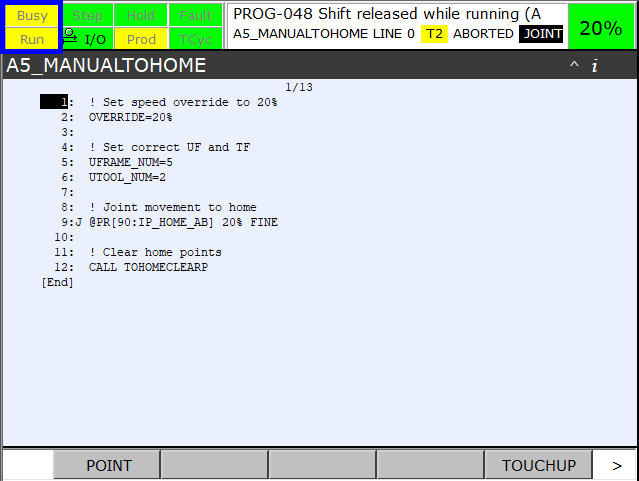
2.5. Switch back to auto mode and reboot the robot
Put the three-position switch on the Robot Controller to AUTO-Mode.
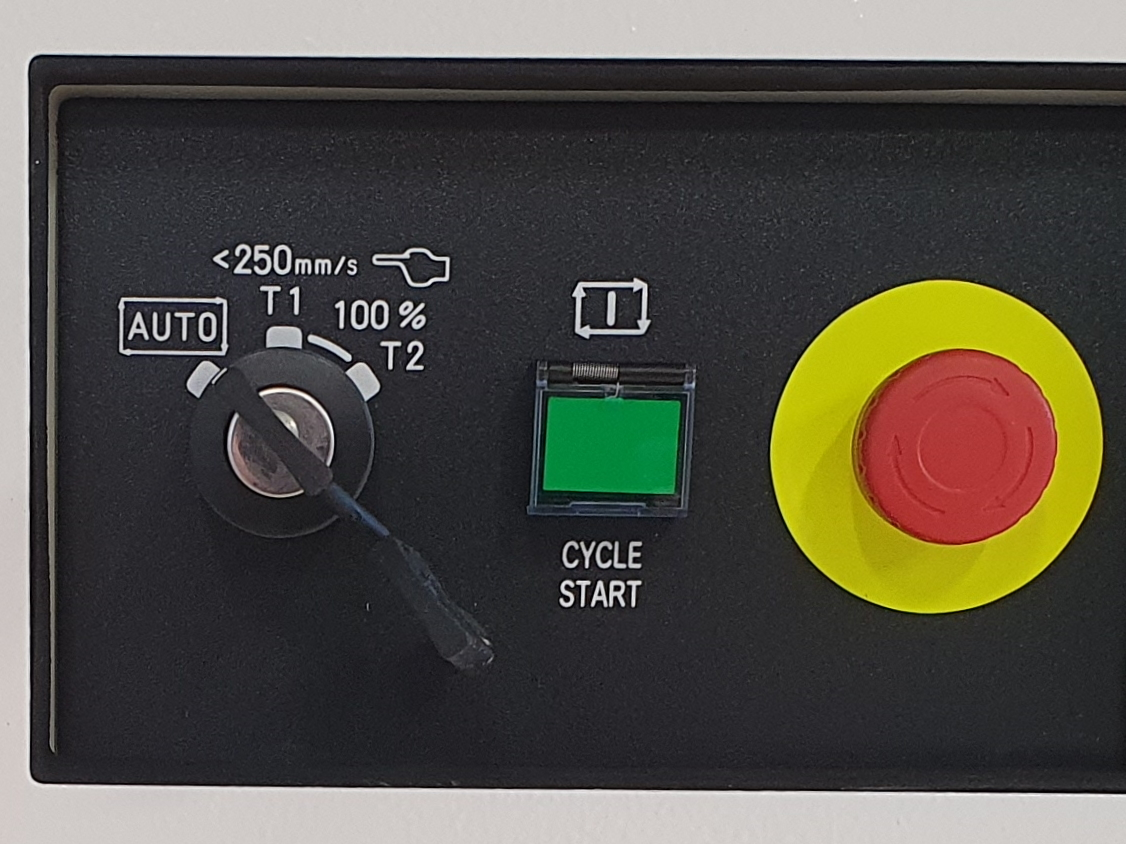
Put the two-position switch on the Teach Pendant to OFF-Mode.
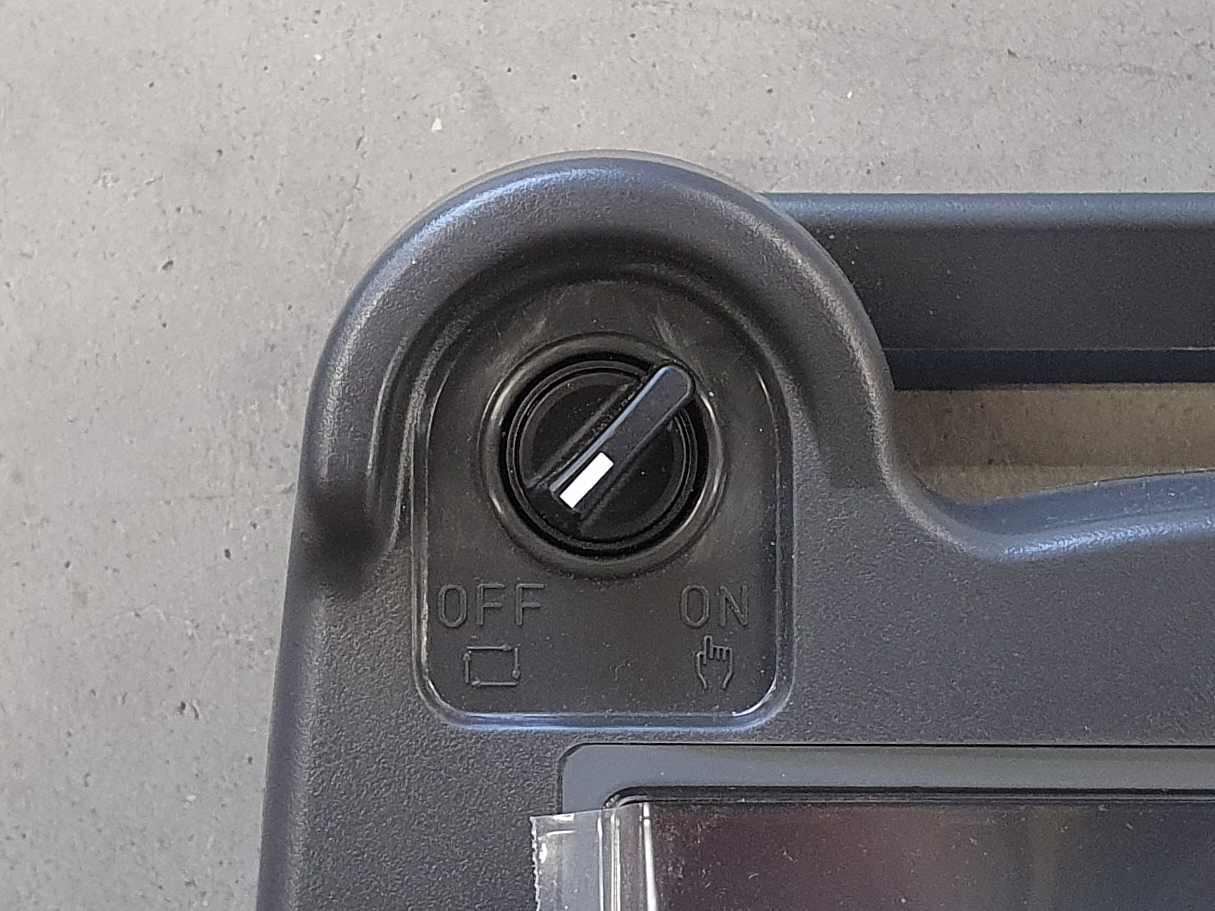
Before rebooting check that the indicator Step is green. Use STEP to toggle step mode.
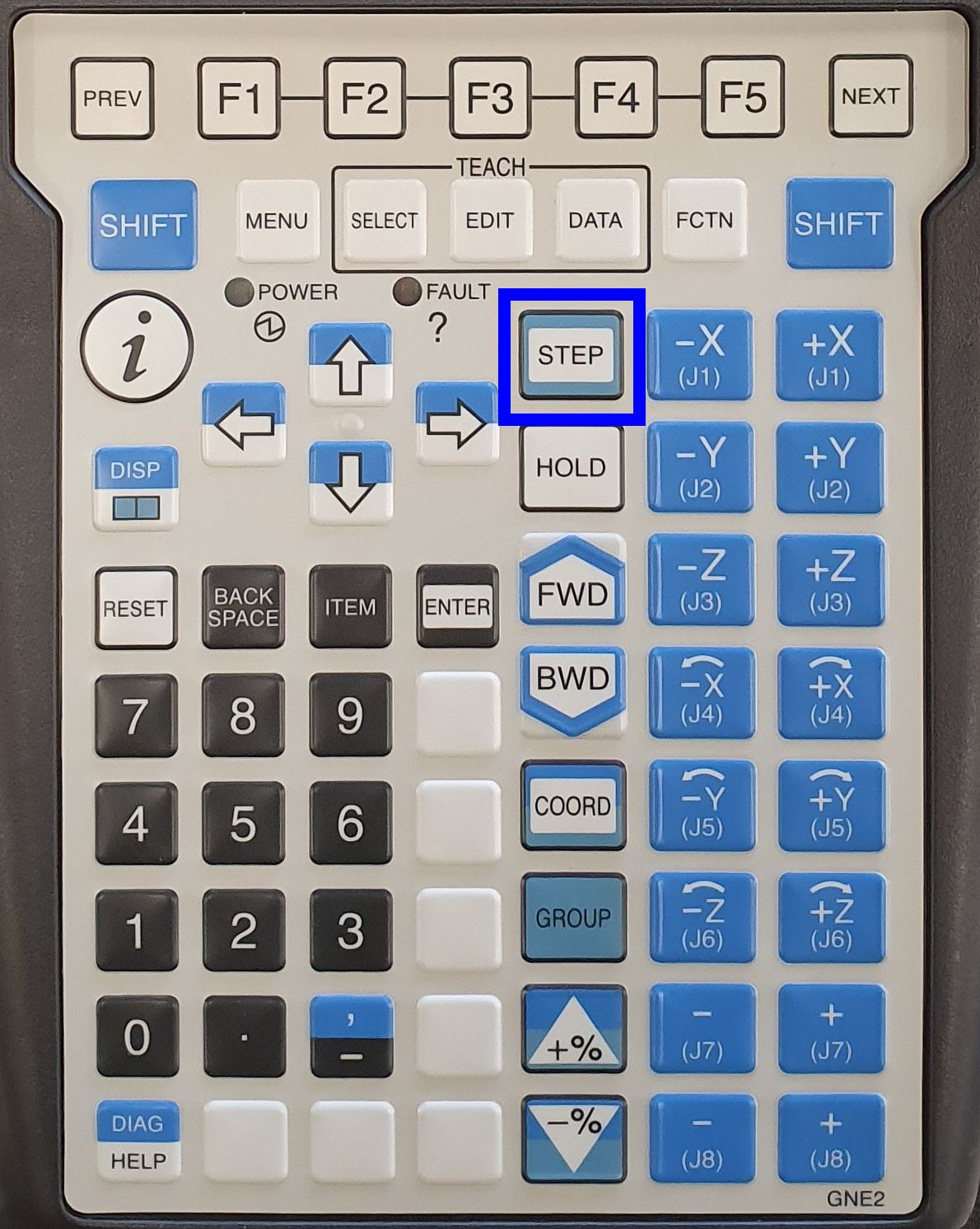
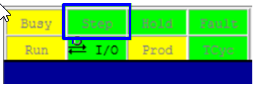
Cycle the power on the robot controller to restart the robot communication software.
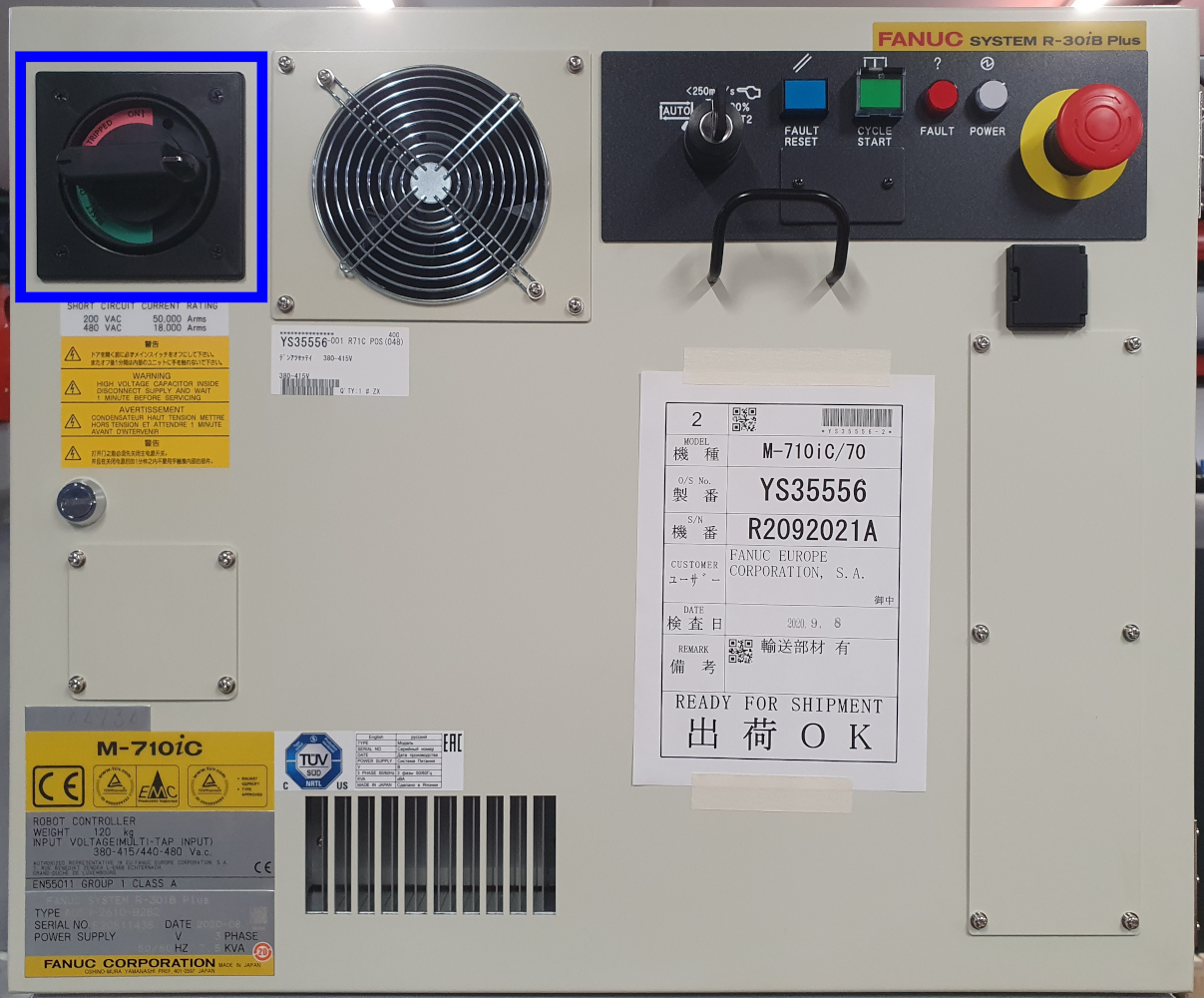
3. How to get further help
Do not hesitate to contact us when you need additional support beyond the documents provided in the RoboJob Service Knowledge Base.
You may contact the RoboJob Service department using following means:
-
Help Center: service.robojob.eu
-
Email: service@robojob.eu
-
Phone: +32 15 70 89 70
We kindly ask you to provide us the following information:
-
Serial number xx-xx-xxx
-
Description of the fault or defective part
-
Exact error code or message
-
What did the robot do
-
What was the robot supposed to do
-
Pictures or videos
You can send this information to us via email.To send large files you may make use of a file transfer service like WeTransfer: robojob.wetransfer.com.
An automatic confirmation will be sent upon receipt of your mail.