Prepare robot for transport
![]() |
The robot has to be moved manually to the home position. This document describes the procedure. |
- 1. Use following tools
- 2. Procedure
- 3. How to get further help
1. Use following tools
|
|
2. Procedure
2.1. Put the Robot in manual mode
Put the three-position switch on the Robot Controller to T1-Mode.
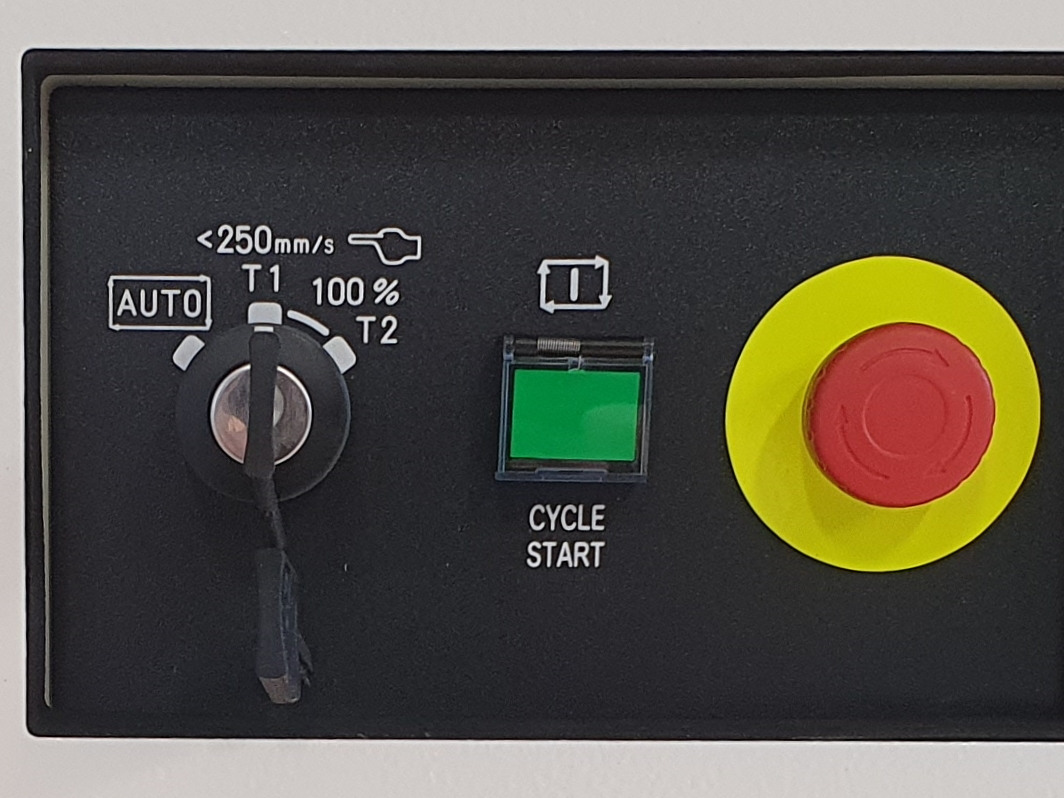
Put the two-position switch on the Teach Pendant to ON-Mode.
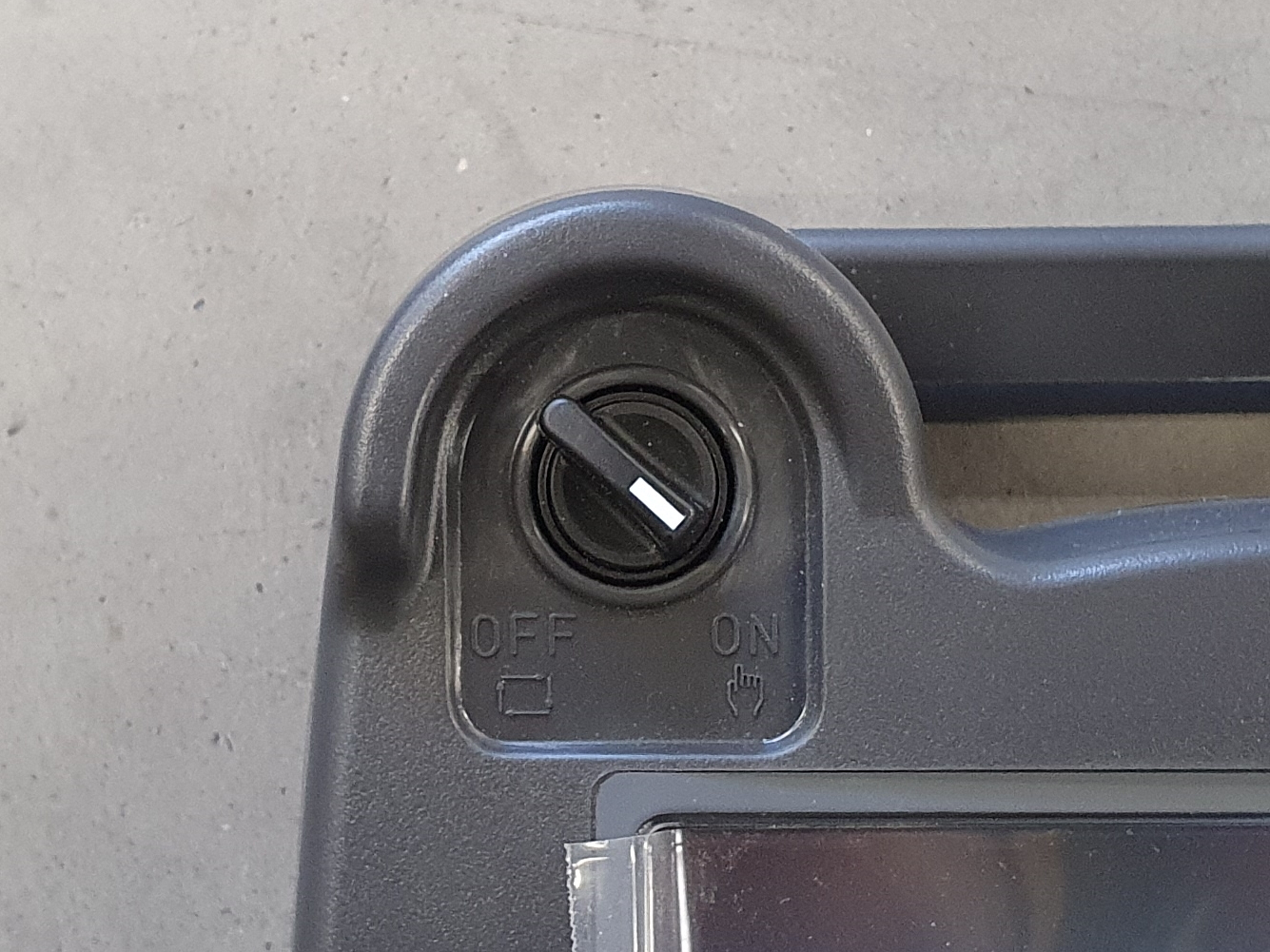
2.2. Abort all the running programs
RoboJob communication programs are still running on the robot.
Abort the running programs by pressing SHIFT + USER KEY 1. The USER KEY 1 is the first key underneath ENTER, sometimes also referred to as Unmarked key 1, Tool 1 or Unnamed 1. On newer versions of the Teach Pendant this key is a blank white key. On older versions of the Teach Pendant this button is the blue WELD ENBL button.
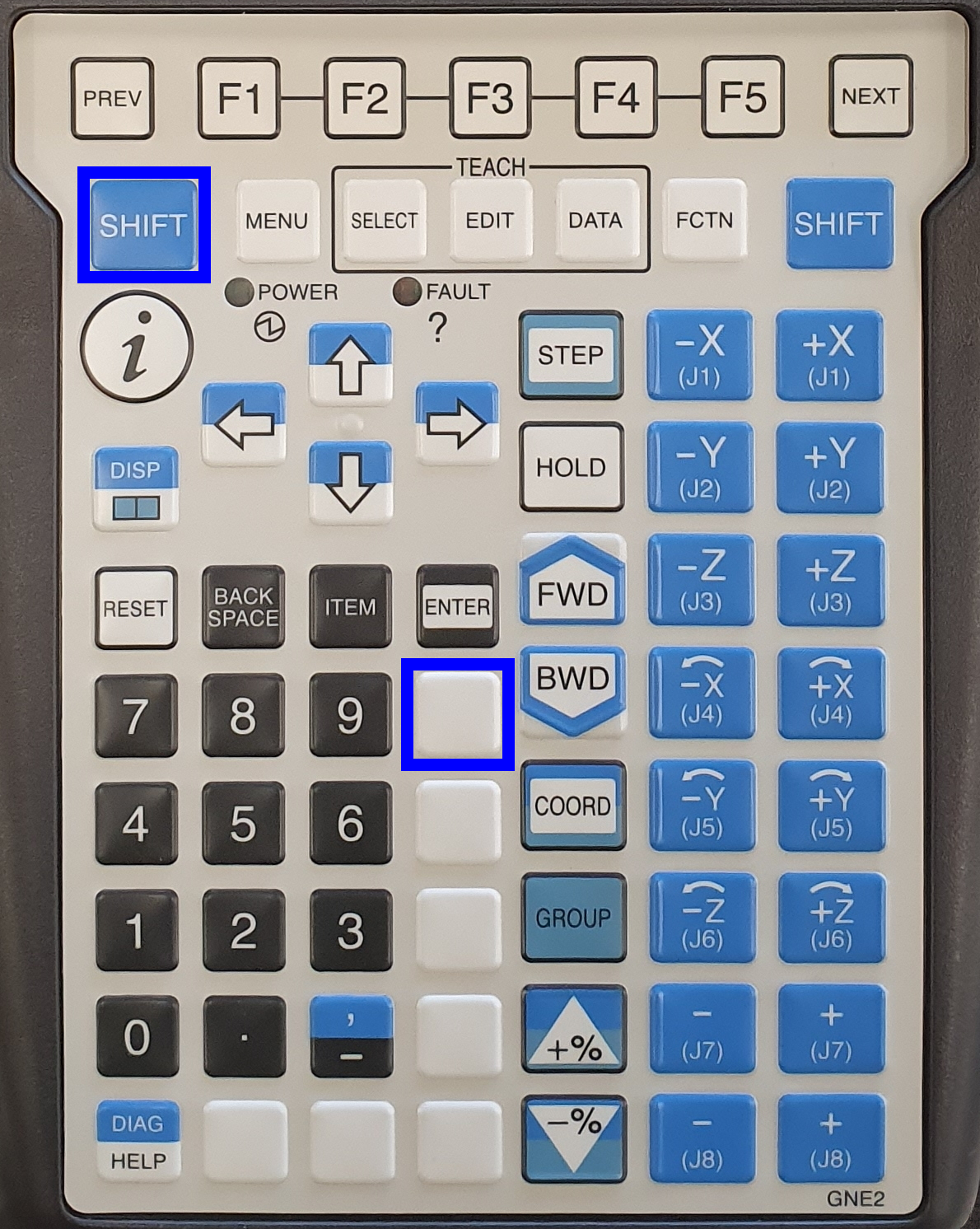
Verify that the software is stopped. The indicators Busy and Run on the top left of the screen should be yellow.
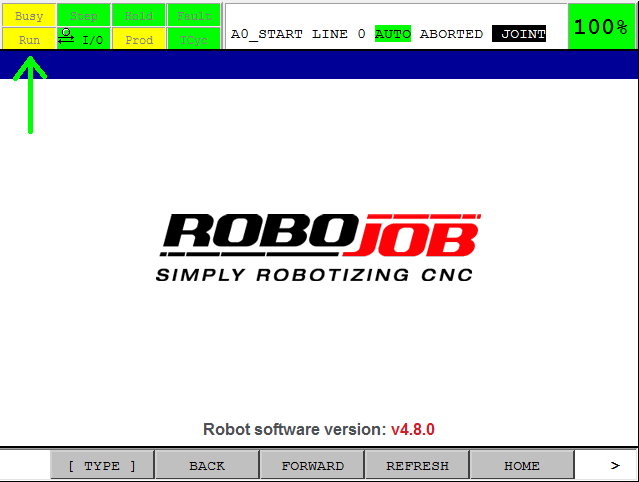
2.3. Reset all Faults and move the robot manual nearby his Home Position
To move the robot in a safe way, one deadman switch on the back of the Teach Pendant must be in the safe middle position.
Both deadman switches have 3 positions:
-
Not pressed
-
Safe middle position
-
Fully pressedTry if you can feel the three positions. To be able to reset the error and move the robot, only one of the two deadman switches has to be in the safe middle position. So don’t push too hard or too soft!
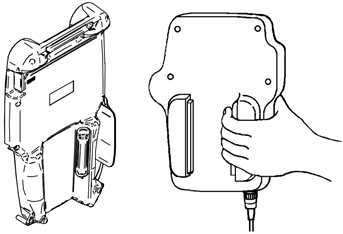
Press SHIFT + RESET to clear all faults. Fault indicator will change to green.
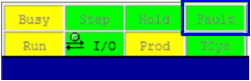
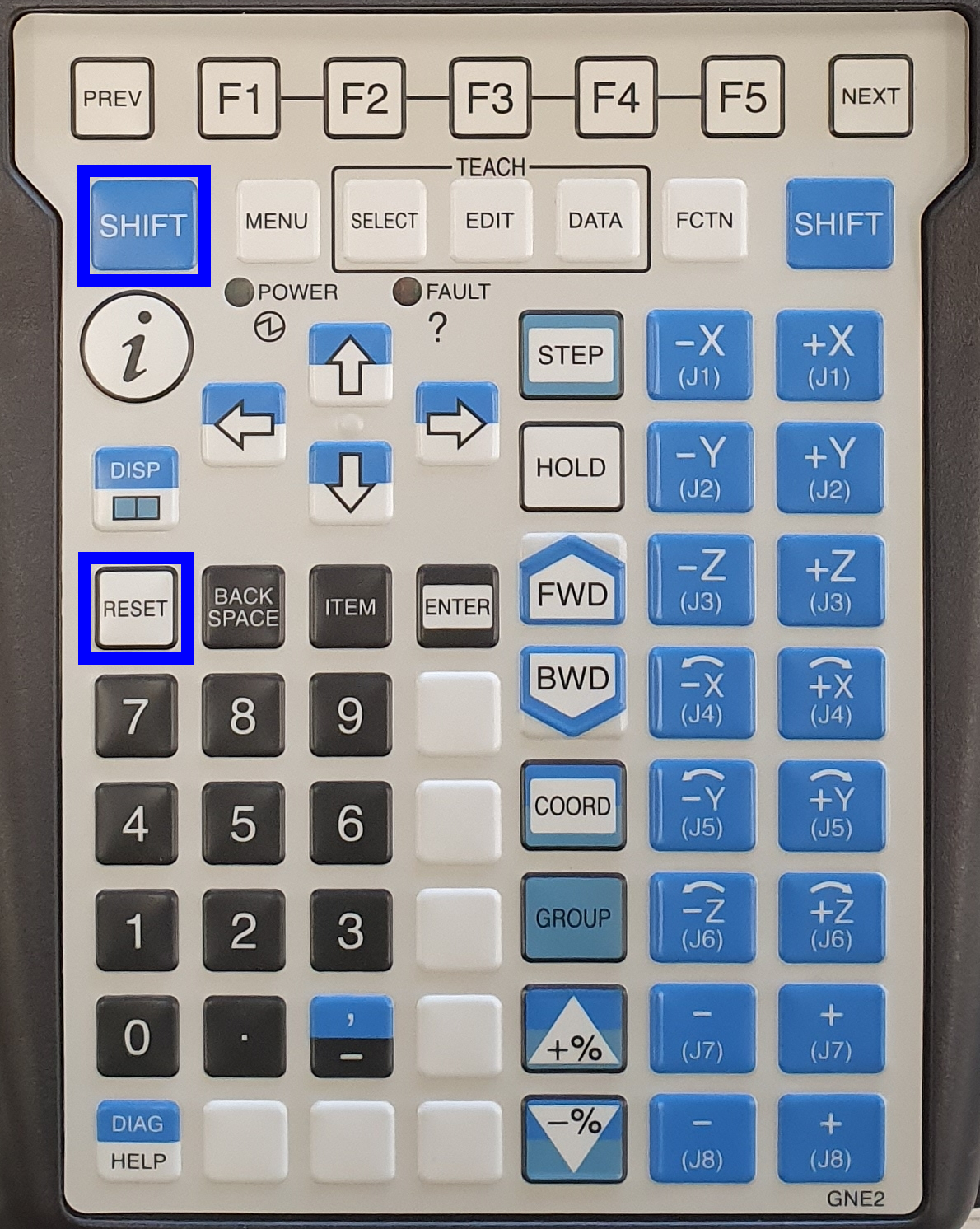
Now you are able to move the robot.
![]() |
Note |
Watch that the robot doesn’t hit anything during the movement. Watch out for other people, surrounding machines, other objects and the robot itself. Make sure the dress out cables around the robot don’t get damaged.
Press COORD to change the way of moving. Keep pressing until JOINT is selected. The JOINT movement mode is the easiest to work with. You move the Joints from the robot one by one.
|
|
Press SHIFT + ±J1-8 to move the robot close to its home position.
|
|
Press SHIFT + +% or -% to adjust the speed.
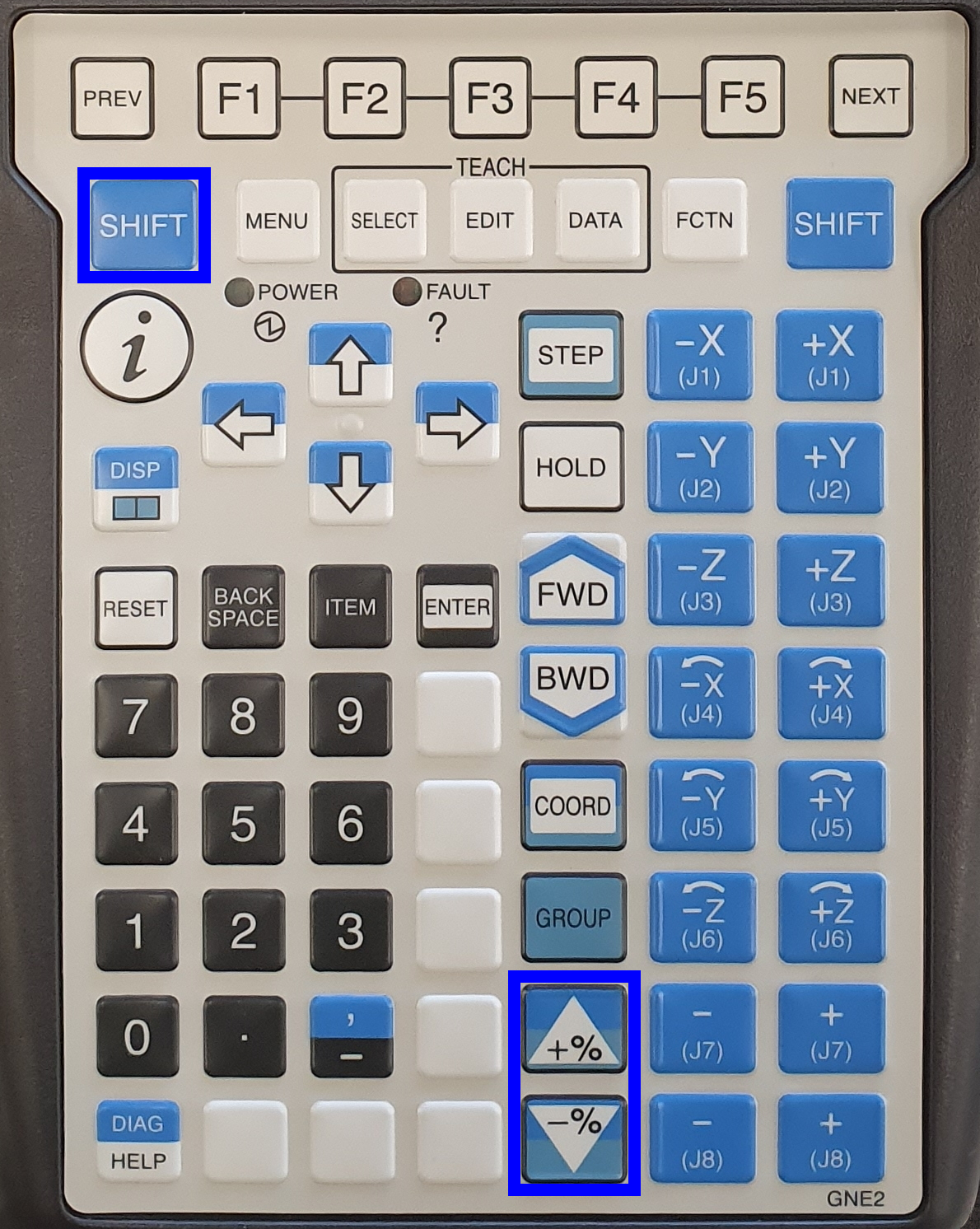
2.4. Execute movement program
Sometimes a utility program can be used to move to a predefined position.
Press SELECT to open the program selection. Use ARROW UP and ARROW DOWN to select the utility program. Hold SHIFT to scroll faster.
When the utility program is selected press ENTER to open the program.
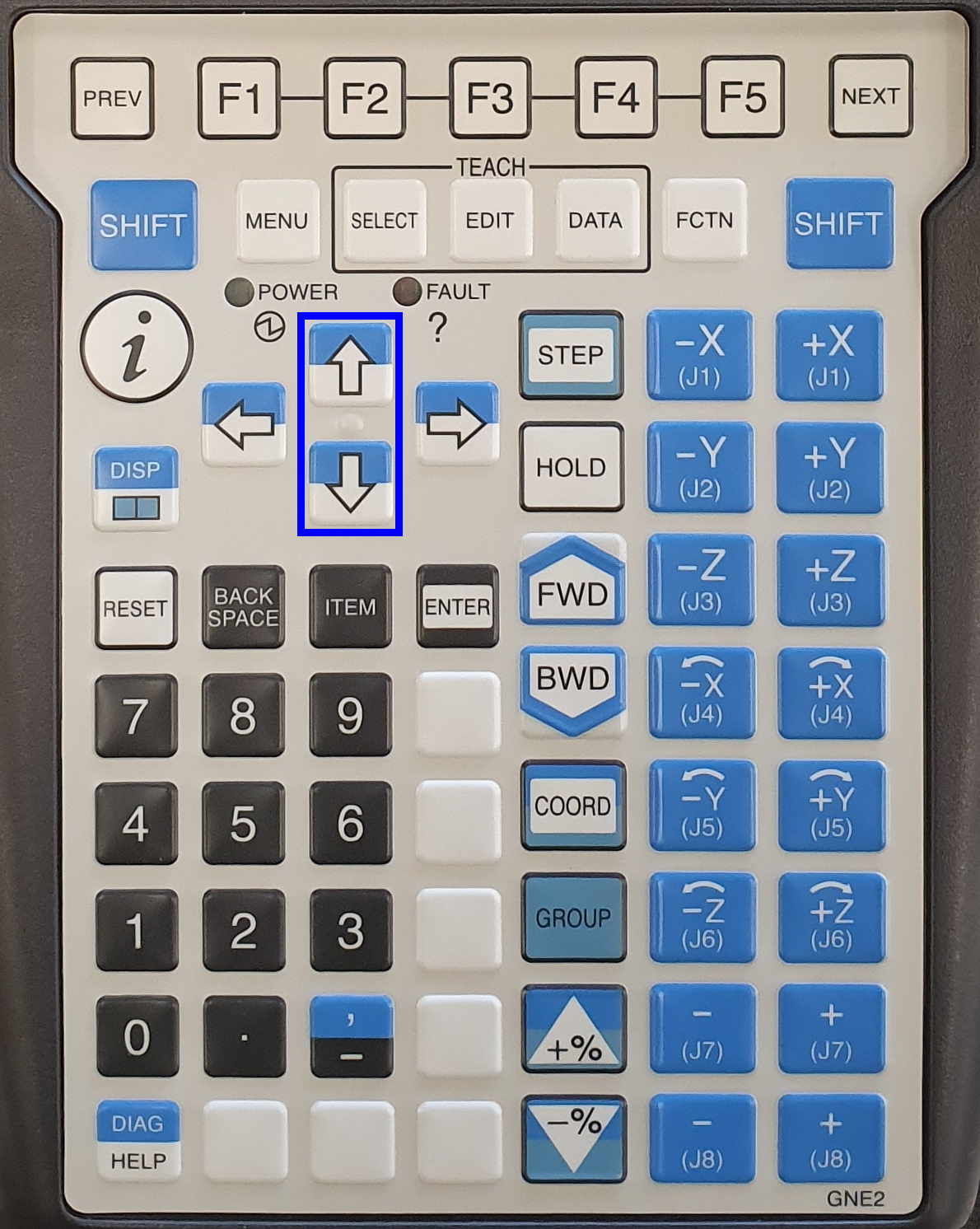
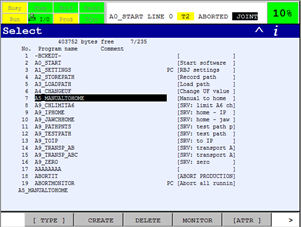
When A5_MANUALTOHOME is selected press ENTER to open the program.Press SHIFT + FWD to execute the program. The robot will execute the movements recorded in the program. Release SHIFT or the deadman switch to stop the movement if needed.
The indicators Busy and Run will become green during the movement. Hold SHIFT and one deadman switch until the program is finished.
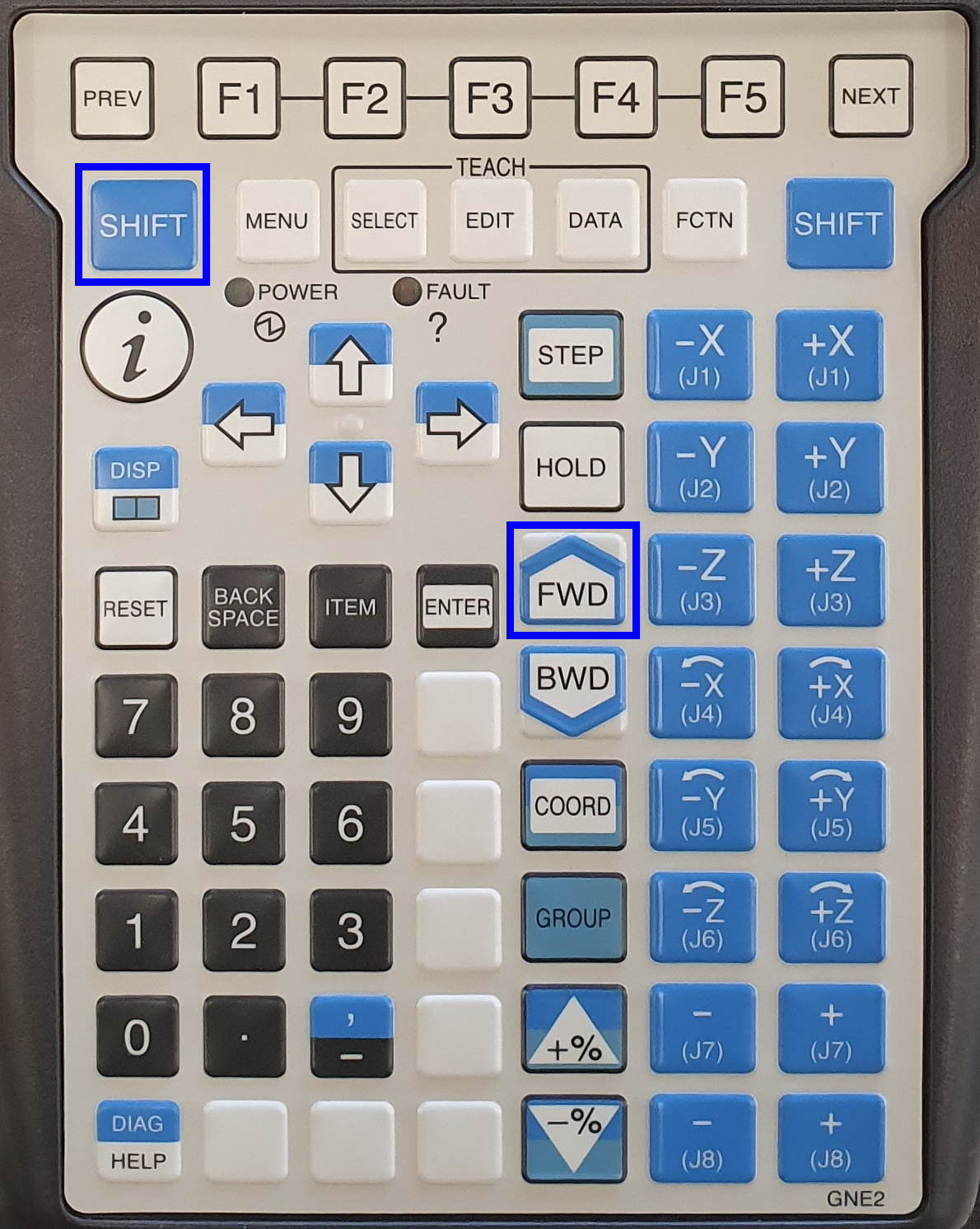
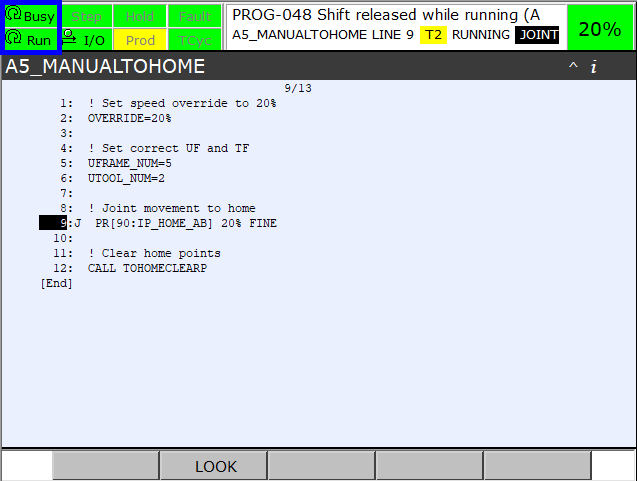
![]() |
Note |
Watch that the robot doesn’t hit anything during the movement. Watch out for other people, surrounding machines, other objects and the robot itself. Make sure the dress out cables around the robot don’t get damaged.
When the robot has reached the home position the indicators Busy and Run will become yellow again and the first line of the program will be selected.
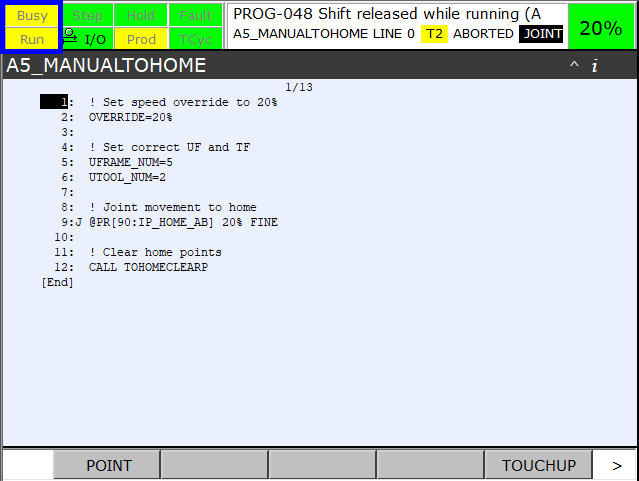
2.4.1. A5_MANUALTOHOME
The program A5_MANUALTOHOME can be used to move the robot to the home position that is teached during the installation. After jogging manually the robot has to be put back in the home position using this program before it can be used again by the software in auto mode.

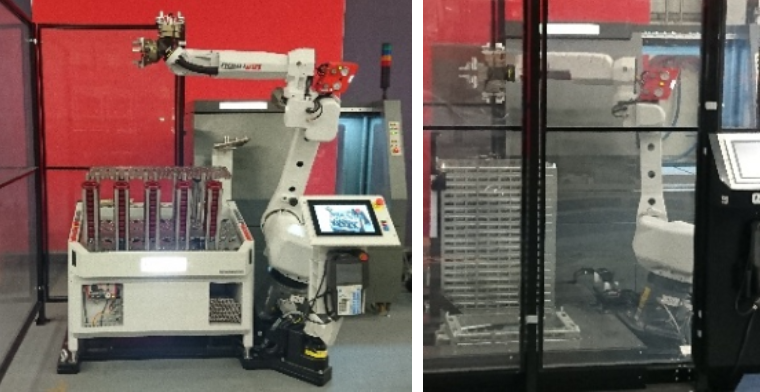
2.4.2. A9_TRANSP_AB
The program A9_TRANSP_AB can be used to put a robot in a good position for transport for robots up to 35kg. When possible use this position to transport the robot on a pallet or on a fixed plate. This position is designed for a robot with 90° gripper heads with A and B gripper. Note how the gripper body is oriented on the pictures below.
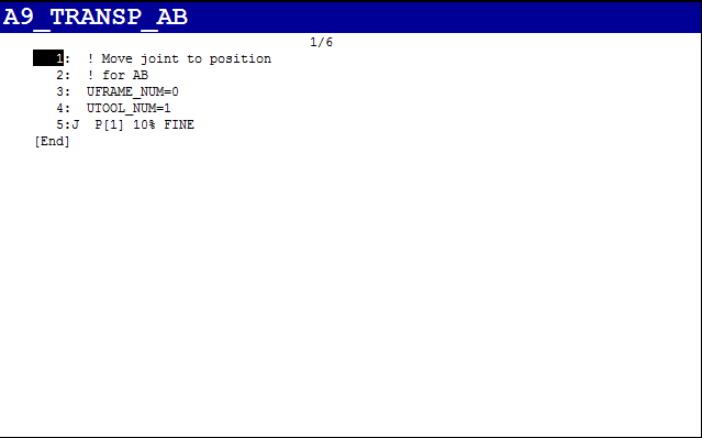
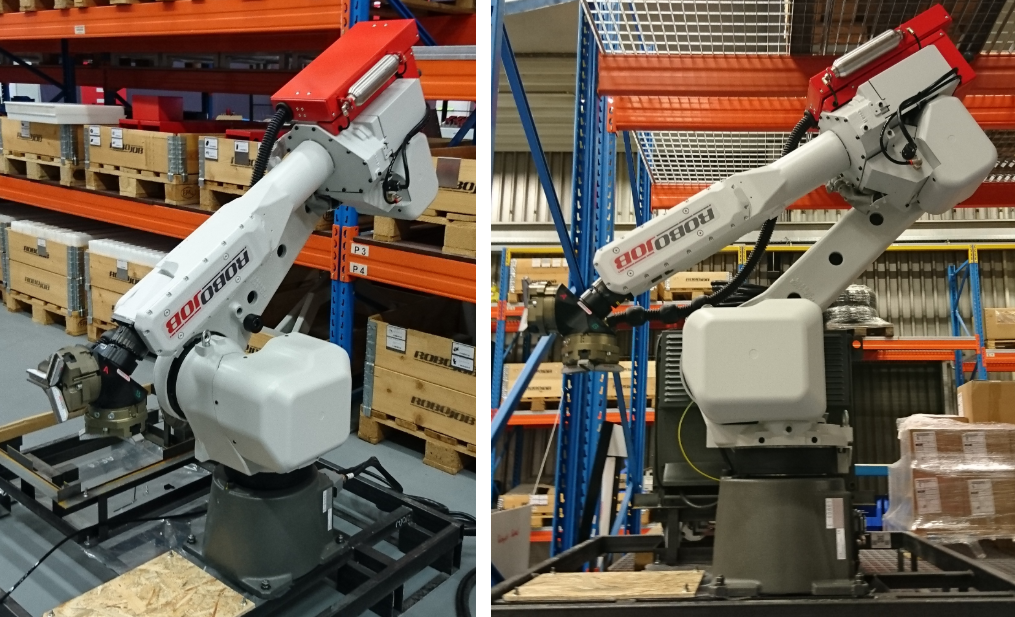
2.4.3. A9_TRANSP_ABC
The program A9_TRANSP_ABC can be used to put a robot in a good position for transport for robots up to 35kg. When possible use this position to transport the robot on a pallet or on a fixed plate. This position is designed for a robot with 180° gripper heads with A, B and optional C gripper. Note how the gripper body is oriented on the pictures below.
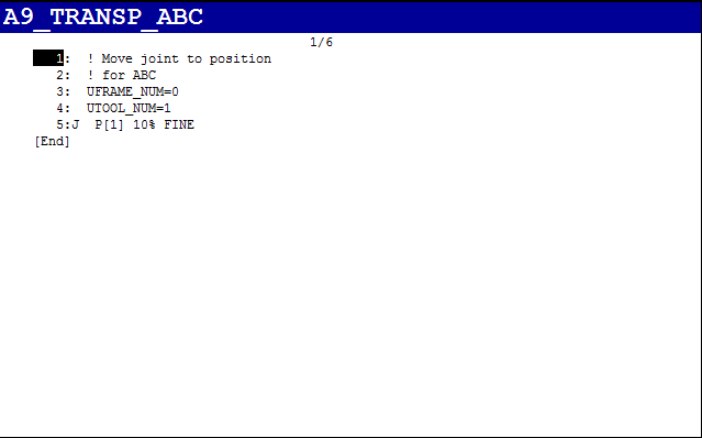
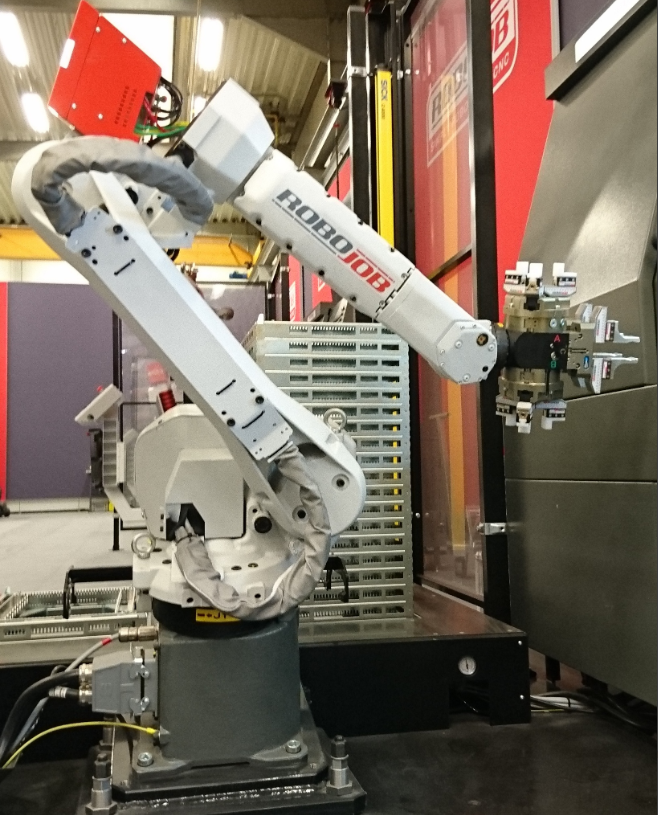
2.4.4. A9_ZERO
The program A9_ZERO can be used to move the robot to a position where all the joint values are zero.
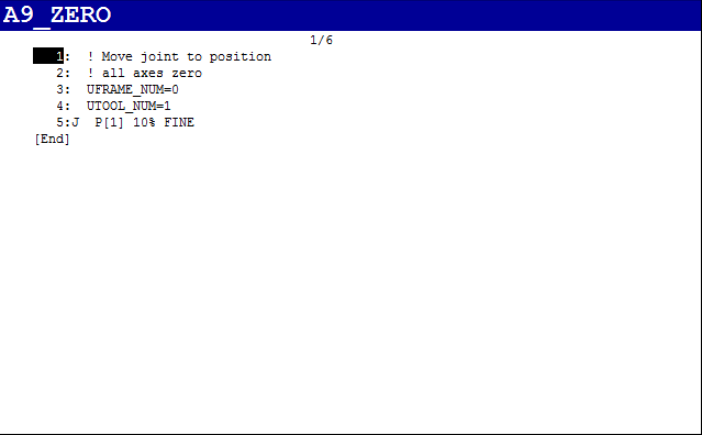
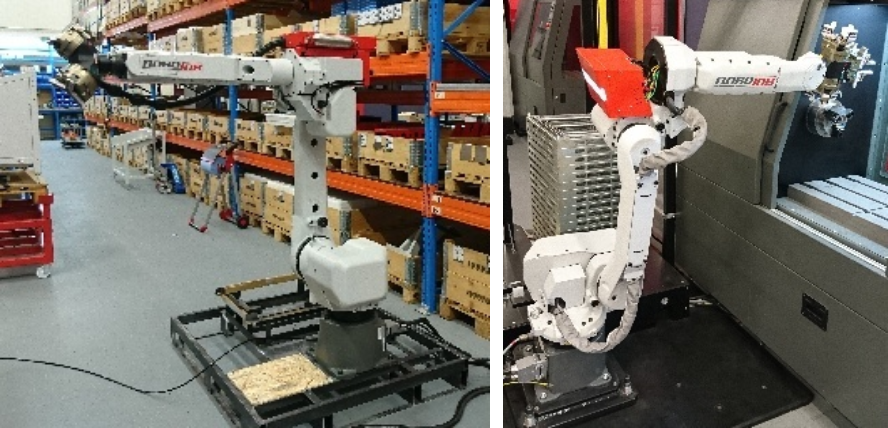
2.5. Remove robot from its support
If the robot is not installed on a base plate, but is anchored ground then the robot has to be dismounted.
2.5.1. Move robot into position
The first step is to move the robot to the correct position to attach the slings. In this example we start from the zero position using the program A9_ZERO. Executing the program will move the robot to a position with all joints values equal to zero. The robot arm will be in a horizontal orientation.
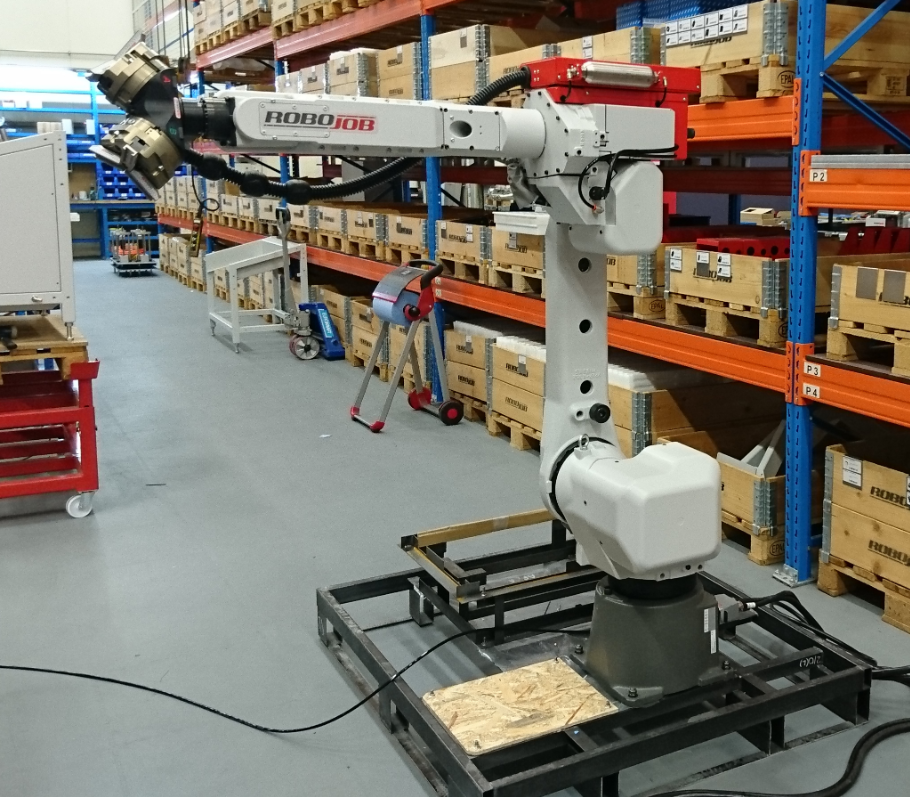
Move J2 until the robot is in the position indicated in the image below. The front of joint 3 will be at the same position as the back of joint one as indicated by the green line.
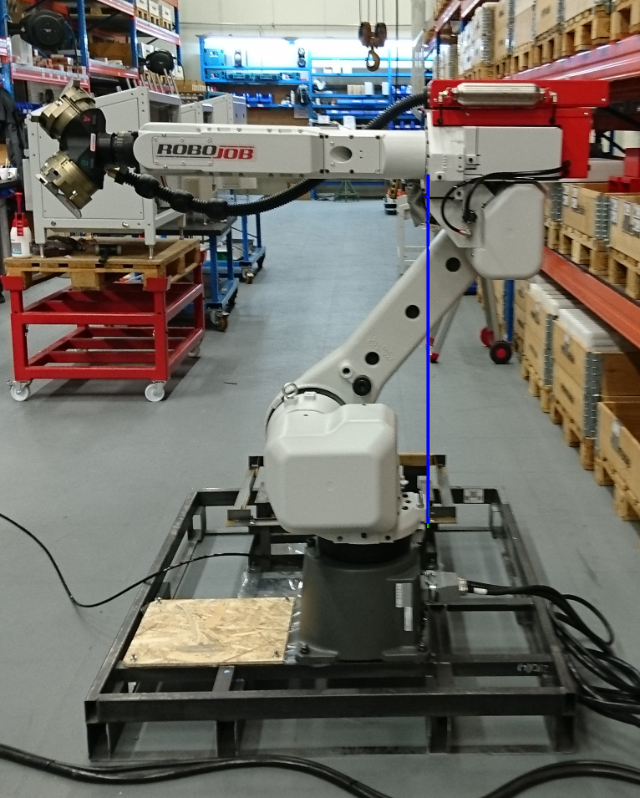
![]() |
Note |
It is not alway possible to reach the zero position, but the robot can manually jog to a good position to attach the slings.
2.5.2. Attach slings
Attach the lifting sling to the lifting eye bolts.
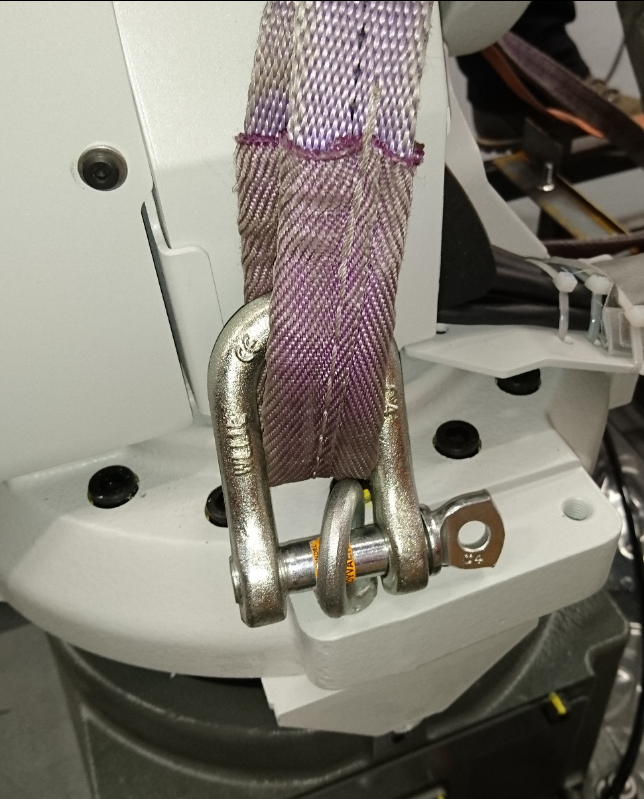
The sling goes in between axis 2 and axis 4.
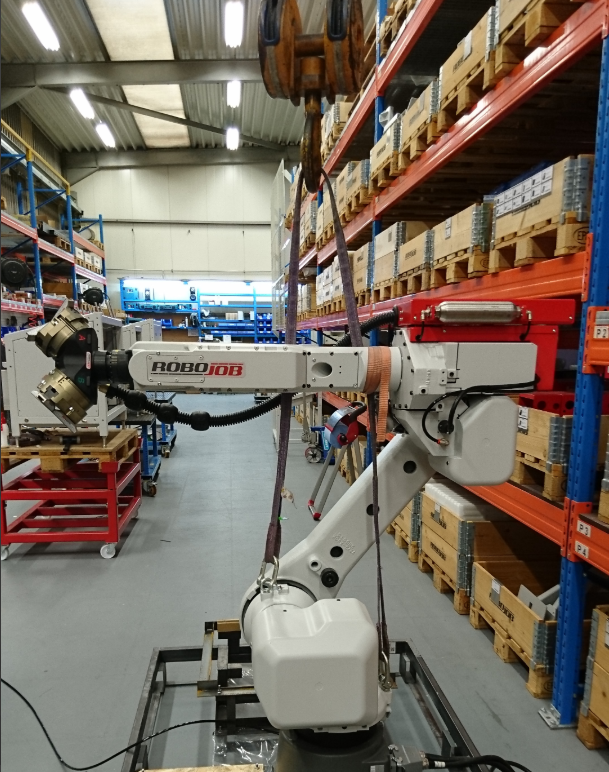
To prevent the robot from tipping over while it is lifted, an extra sling used to attach the sling to axis 4.This will put alot of stress on the sling as the weight of the robot it leaning against it.Make sure your slings can handle te forces.
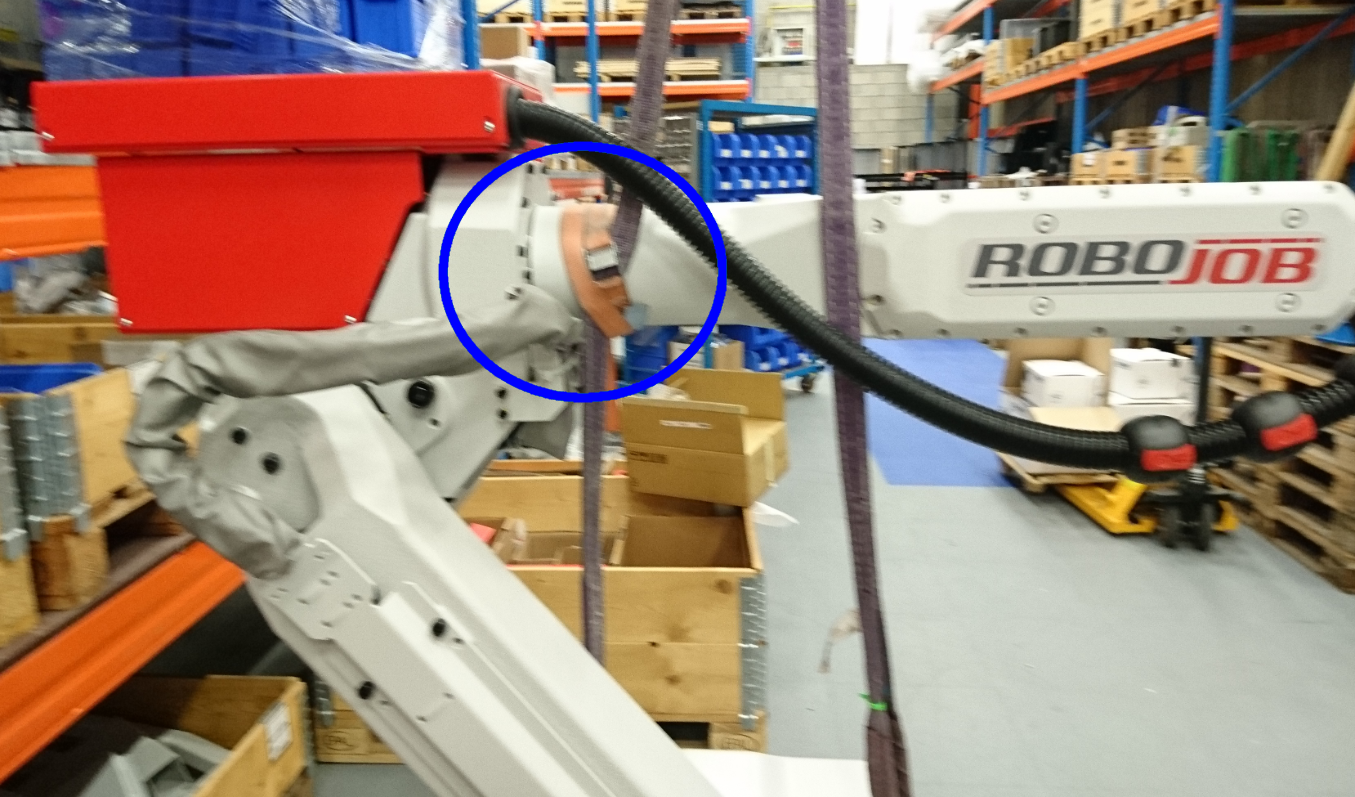
2.5.3. Disconnect cables and air supply
Before lifting the robot, make sure to remove the cable to the controller, the air supply and the ground cable. Remove any additional cables that are attached to the robot via the base. Leave the batteries in the robot and leave the cables on the robot arm attached. The batteries will power the encoders on the motors so that the robot remembers its position.
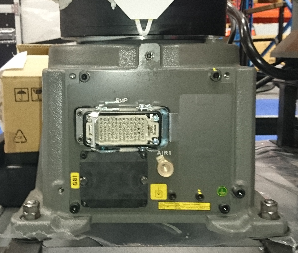
2.5.4. Lift the robot from the robot support
Remove the nuts from the bolts on the robot support. Carefully lift the robot robot from its support. Bolt the robot on a pallet for transportation.
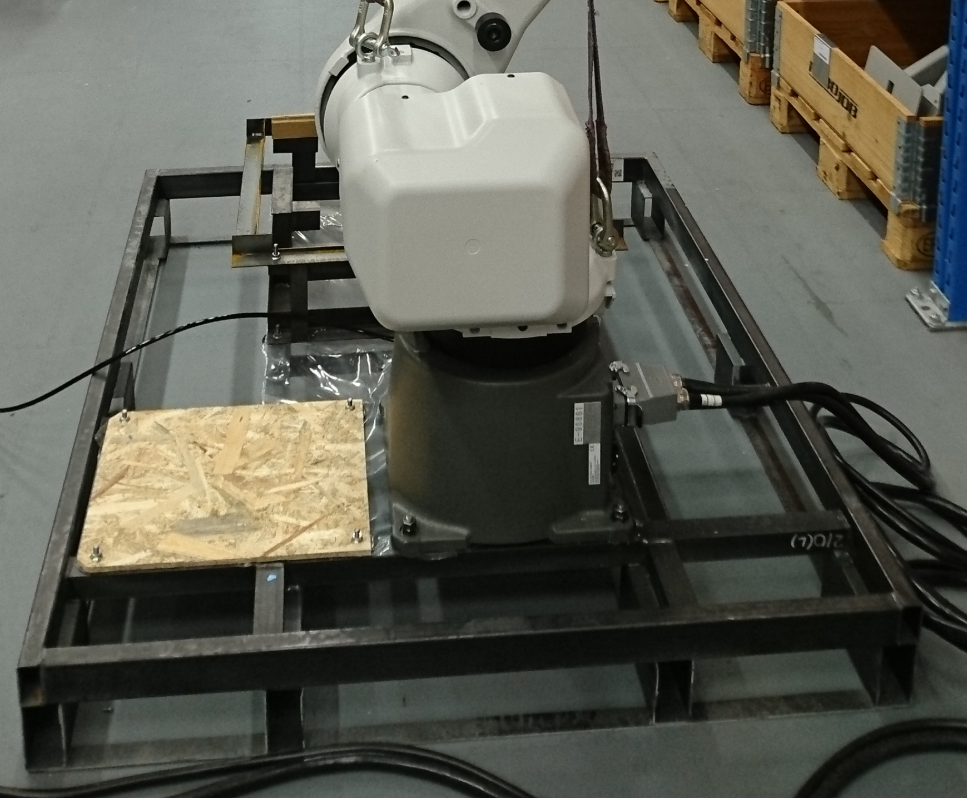
2.6. Prepare robot for transport
When the robot is on a base plate, the complete installation can be moved without taking the robot of its support. When the robot is not on a base plate the robot has to be bolted to a pallet for transport.
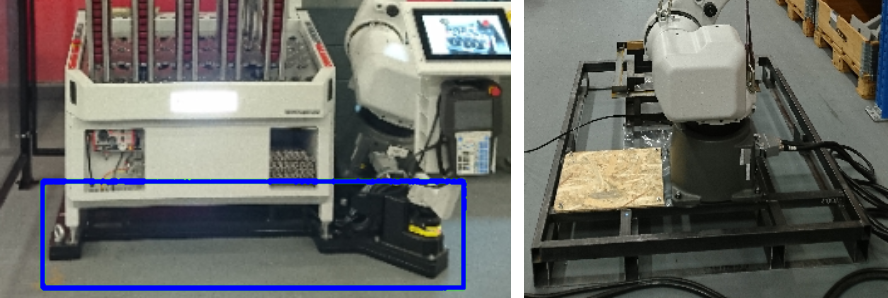
In both cases the robot has to be moved to its transport position. If the cable to the controller was detached, then reattach it so we can jog the robot. Use the programs A9_TRANSP_AB or A9_TRANSP_ABC, depending on the gripper body, to move the robot to its transport position. If the program can not be used or the position is unreachable, then jog the robot manually to a similar position so that the robot is safe for transport.
Wrap the robot in bubble wrap and plastic to protect it during transport.
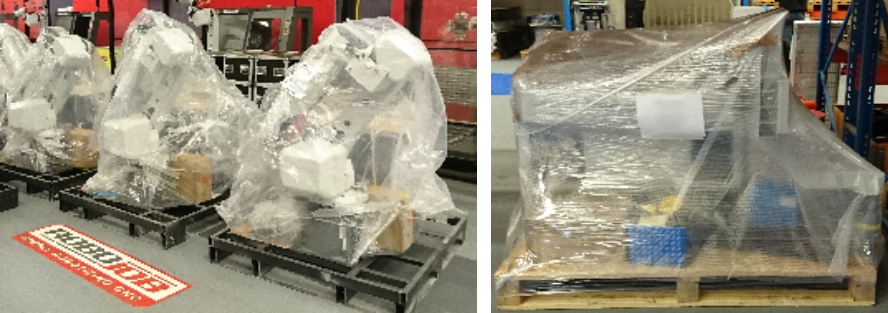
![]() |
Note |
Do not try to dismantle any other part of the robot. Do not remove the batteries from the robot. Do not disconnect the motors or the encoders from the robot.
![]() |
Note |
Only move the robot using the controller. Do not try to move the robot manually.
3. How to get further help
Do not hesitate to contact us when you need additional support beyond the documents provided in the RoboJob Service Knowledge Base.
You may contact the RoboJob Service department using following means:
-
Help Center: service.robojob.eu
-
Email: service@robojob.eu
-
Phone: +32 15 70 89 70
We kindly ask you to provide us the following information:
-
Serial number xx-xx-xxx
-
Description of the fault or defective part
-
Exact error code or message
-
What did the robot do
-
What was the robot supposed to do
-
Pictures or videos
You can send this information to us via email.To send large files you may make use of a file transfer service like WeTransfer: robojob.wetransfer.com.
An automatic confirmation will be sent upon receipt of your mail.