Troubleshooting connection issues
![]() |
This document explains the troubleshooting steps that can be followed to investigate connection issues.These issues are normally indicated by the error messages: No response from device(s) or Not connected to device(s). |
1. Use following tools
|
|
|
|
|
|
2. Procedure
2.1. Restart all devices
Restart all devices: the IPC, Robot controller, Stacker table, Device Interface and machine.The software might be in an invalid state and can be reset by restarting the device.
After restarting the software, make sure all devices are powered on and running.The software on the IPC should be started after all other devices are ready.
The Turn Assist software only makes connections when it is started.When a connection is lost, the software needs to be restarted.
2.2. Ping test
A ping test can be used to check if the network is configured correctly.A successful ping test means that basic communication is possible with the device.But the network may still be unreliable or there might still be a problem with the software.
Open the on-screen keyboard on the IPC or attach a USB-keyboard.
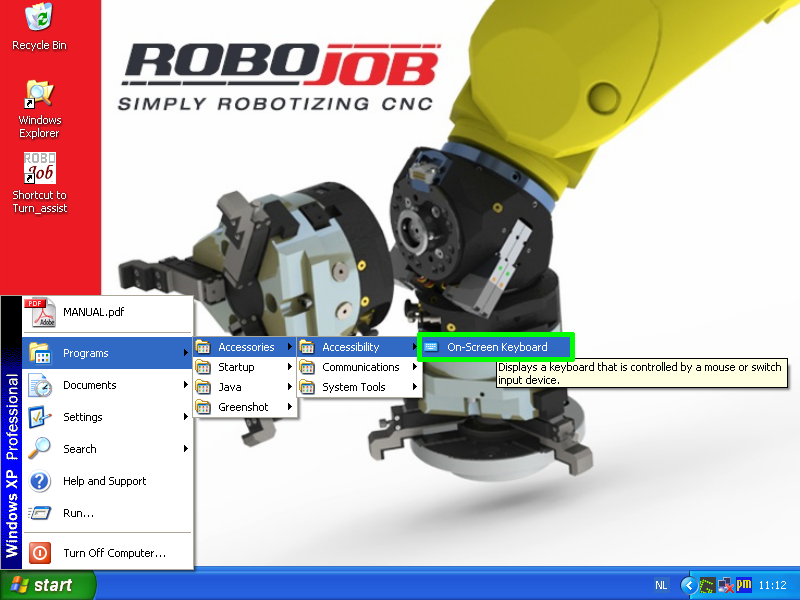
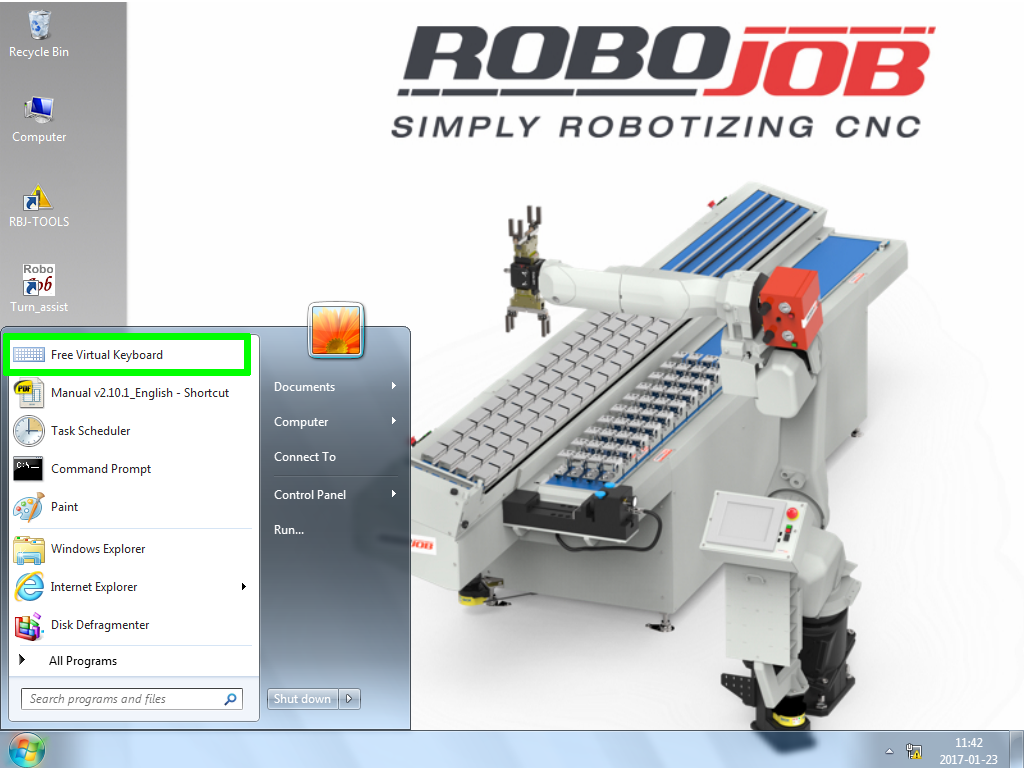
Open menu start end press Run… to open a run window.
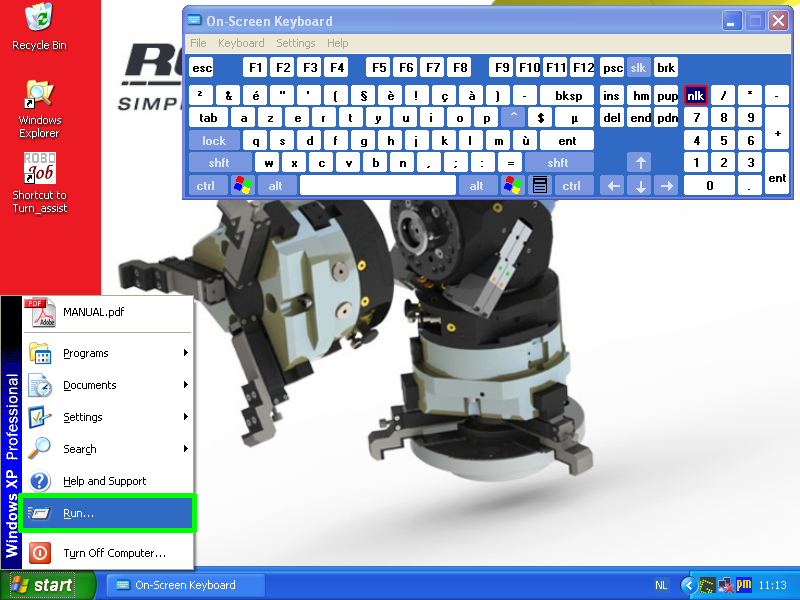
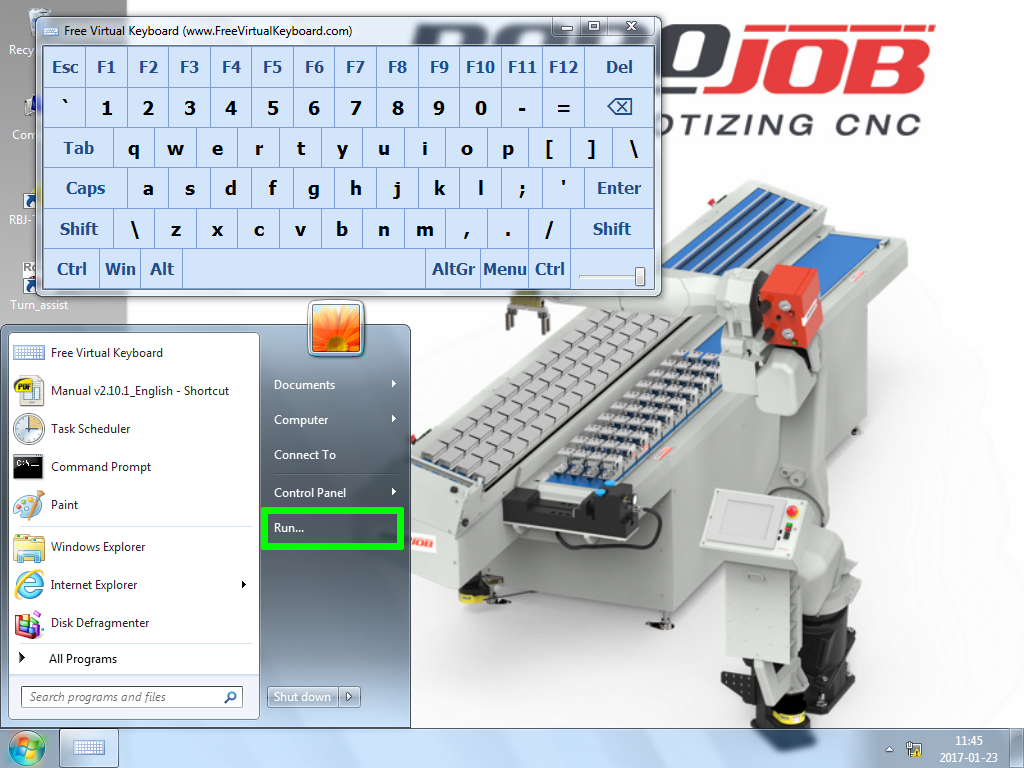
Type cmd.exe and press enter to open a Command Prompt.
Type ping followed by the IP-address off the device you want to test and press enter to ping it.For example type 'ping 192.168.200.9' to check the connection with the robot.
Standard IP-adresses:
Device | Adress |
---|---|
Stacker (IRS-CW) |
192.168.200.10 |
Stacker Motor 1 |
192.168.200.7 |
Stacker Motor 2 |
192.168.200.8 |
Device Interface (Machine) |
192.168.200.6 |
Robot Controller |
192.168.200.9 |
IPC (software console) |
192.168.200.4 |
If there is a response from the device, the output will mention the test results: bytecount, round trip timetime, …This means that basic communication is possible.The issue wil most likely be caused by a software problem.
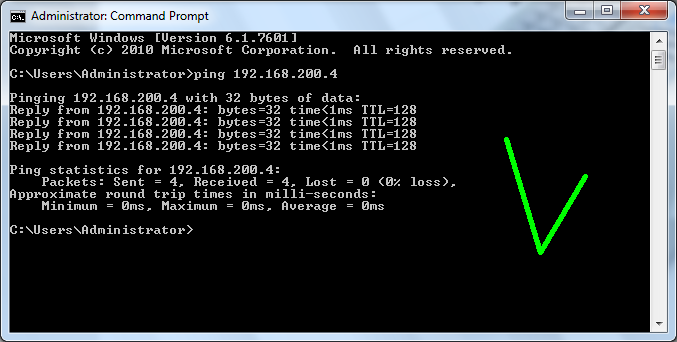
When there is no response, the output will show Destination host unreachable.This means that even the most basic communication is not possible.The problem will most likely be electrical: losse connections, damaged cables, …
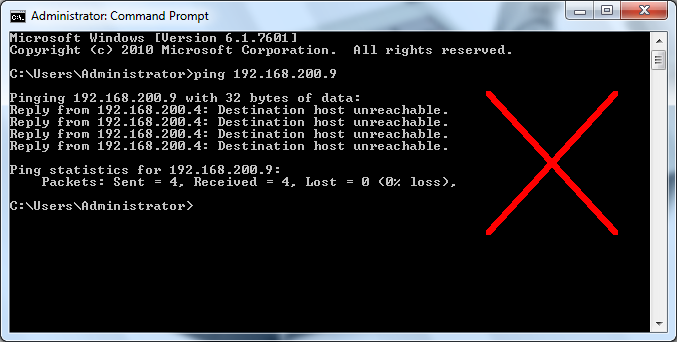
2.3. Verify software configuration
Verify that the IP adresses and port numbers are configured correctly in the software.These settings can only be altered when software changes are made.
2.4. Check ethernet cables
Verify that all cables are connected.Verify that no cables are interrupted, broken or damaged in any way.
All cables are connected to a central Ethernet switch located in the stacker table or in the robot controller.
2.4.1. Stacker Table
Check the Ethernet connections on the exterior of the stacker table.Depending on the setup the number of connections may vary.
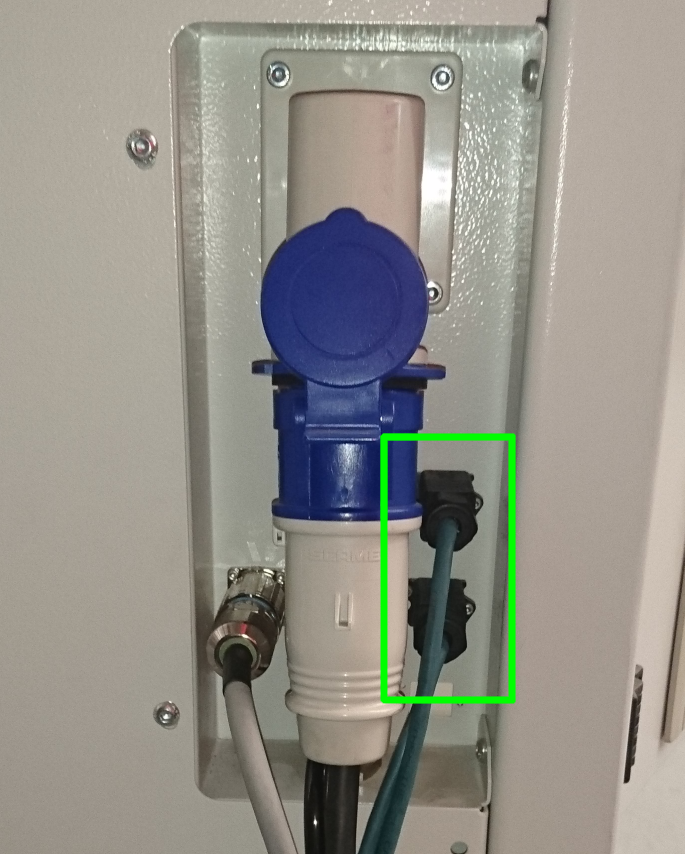
Open the door of the stacker table and check the Ethernet connections inside.
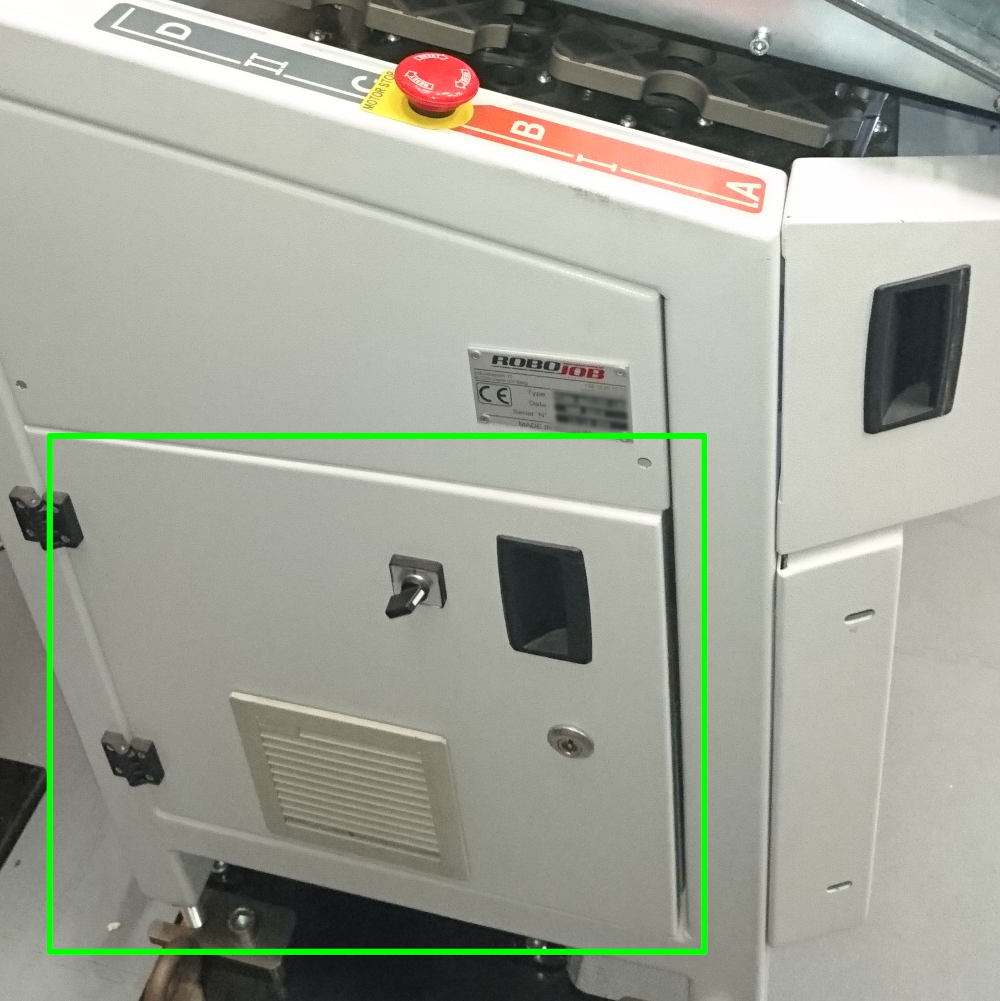
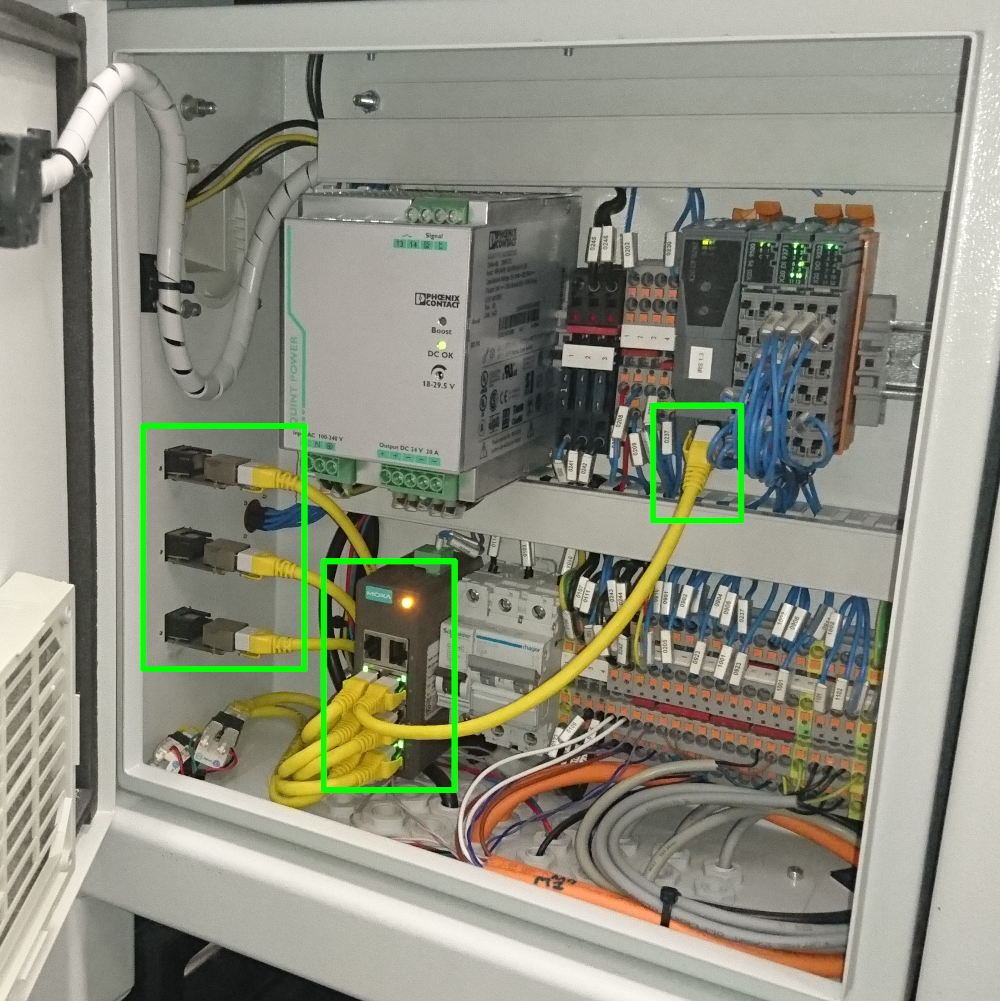
Depending on the setup there might be an Ethernet switch inside the stacker table.Try moving the connections in the switch one by one.Check if the indicator lights are on or blinking.
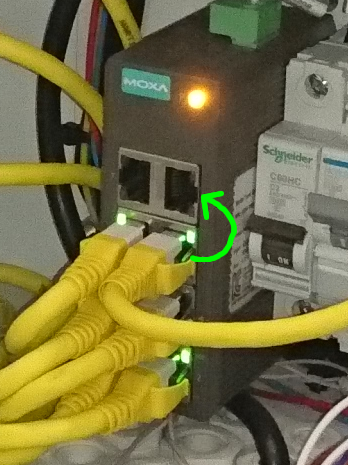
2.4.2. Device Interface PLC
Check the Ethernet cable at the device interface.The Device Interface is a PLC used to communicate with the machine.It is normally integrated into the machine or located in a small seperate electrical cabinet close to the machine.
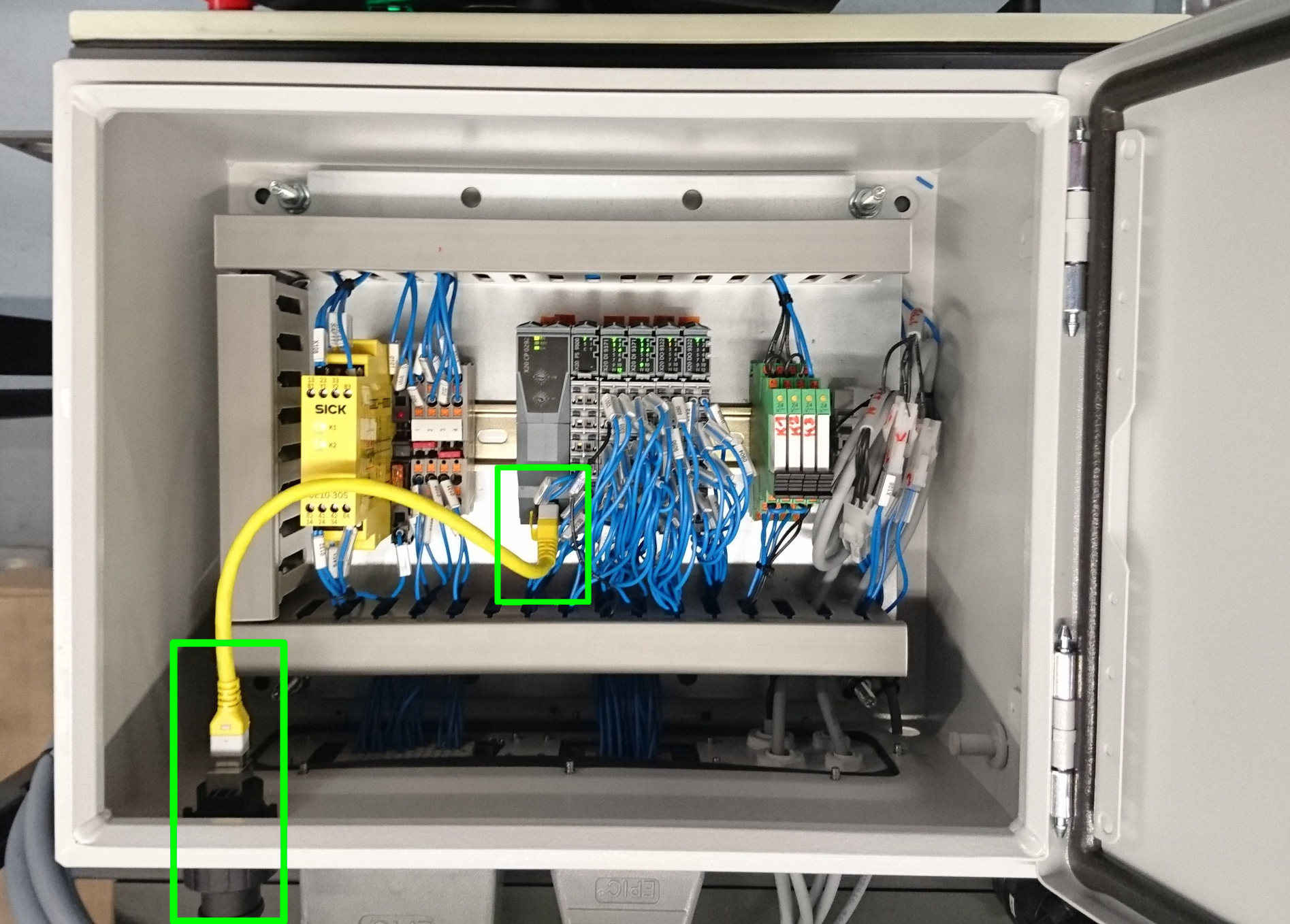
2.4.3. Robot
Open the door of the robot controller and check all Ethernet connections inside.Make sure the Ethernet cable is connected to the correct port.
Depending on the setup there might be an ethernet switch inside the robot controller.
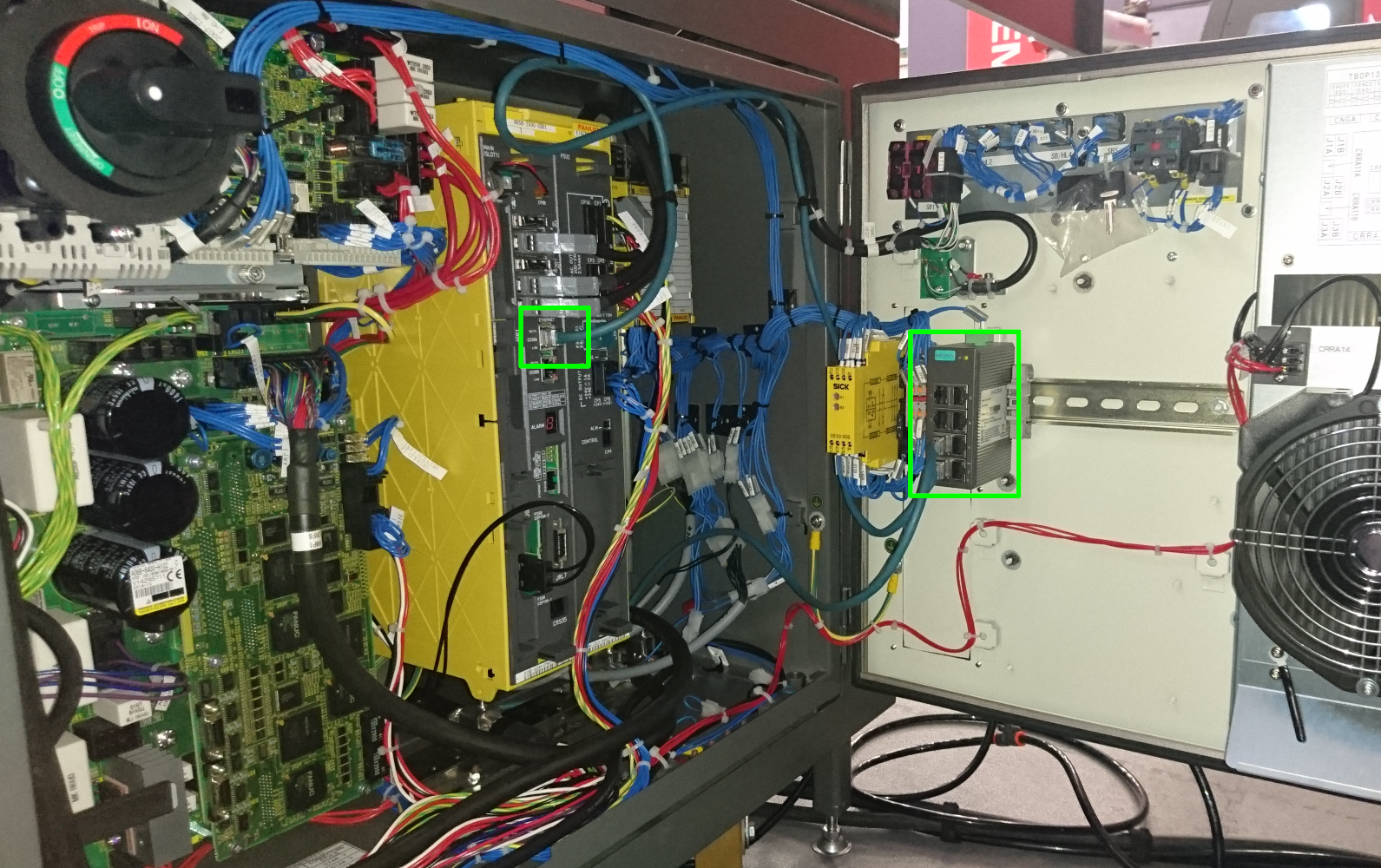
2.4.4. IPC
The IPC can be dismounted by removing the six hex bolts on the sides of the screen.Check that the ethernet cable is connected to the correct ethernet port.Please note that you must plug the ethernet cable back into the IPC port it was originally installed in.The IPC ports are seperate NIC’s, they are not switched!
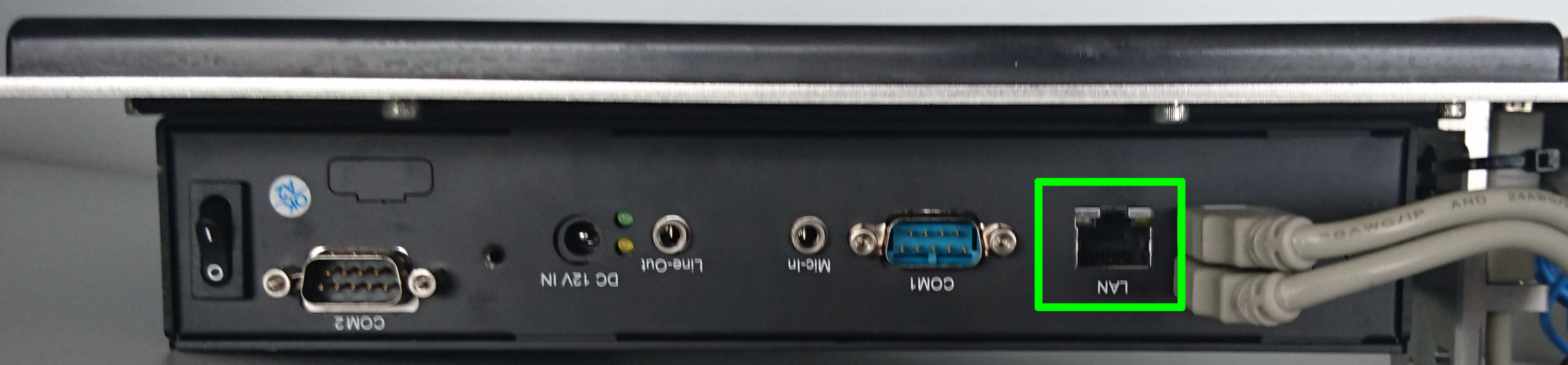

2.5. Use a cable tester
Use a LAN cable tester to check all Ethernet cables.Refer to the manual of the cable tester for instructions on how to use it.This test will check if the Ethernet cables themselves are wired correctly.
2.6. Replace cables
Replace all cables that fail one of the tests above.
If the test above succeed but there are still intermittent problems with the connection, try replacing the cable with a temporary cable that is known to function correctly.This temporary cable can be routed around the machine, just for testing.If the connection problems still recur then they are for sure not caused by the cable.
3. How to get further help
Do not hesitate to contact us when you need additional support beyond the documents provided in the RoboJob Service Knowledge Base.
You may contact the RoboJob Service department using following means:
-
Help Center: service.robojob.eu
-
Email: service@robojob.eu
-
Phone: +32 15 70 89 70
We kindly ask you to provide us the following information:
-
Serial number xx-xx-xxx
-
Description of the fault or defective part
-
Exact error code or message
-
What did the robot do
-
What was the robot supposed to do
-
Pictures or videos
You can send this information to us via email.To send large files you may make use of a file transfer service like WeTransfer: robojob.wetransfer.com.
An automatic confirmation will be sent upon receipt of your mail.