Calibrate TA table height - Multi-Assist (gen 1 table)
![]() |
This document describes how to calibrate the stacker table height.The table needs to be re-calibrated after modifications have been made to the mechanical or electrical part of the table system. |
1. Use following tools
|
|
|
2. Procedure
2.1. Align and measure the table height
Measure the height of the table close to the support bars, it is measured from the top of the support pillars.Remove all other pillars and use the same pillar for all measurements to avoid measuring errors.
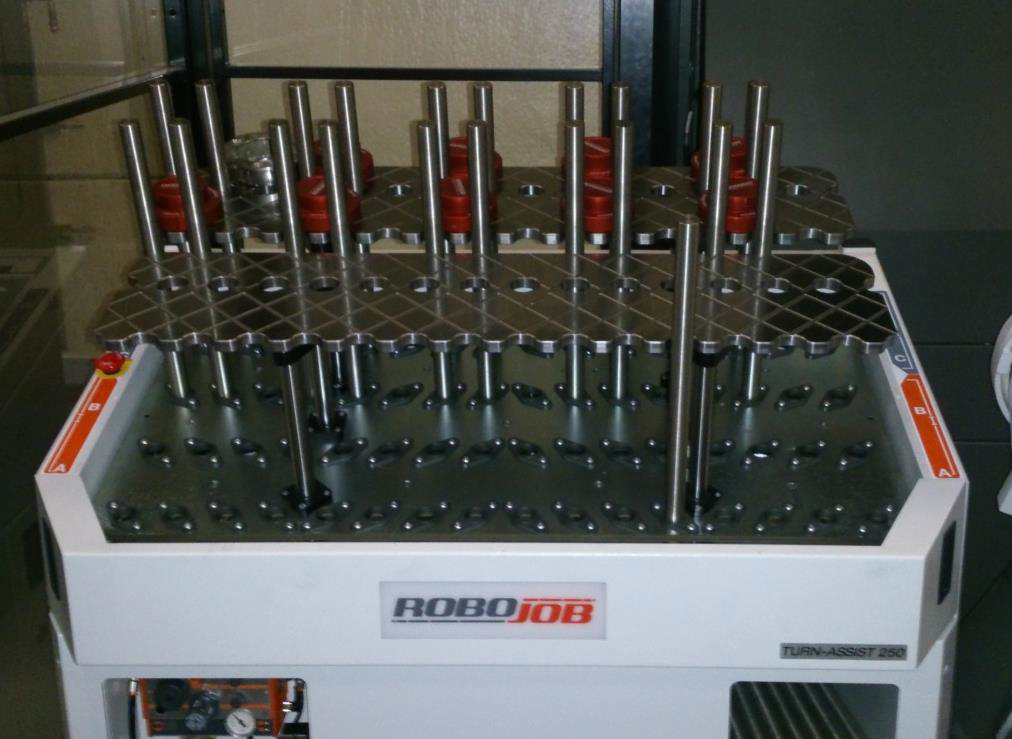
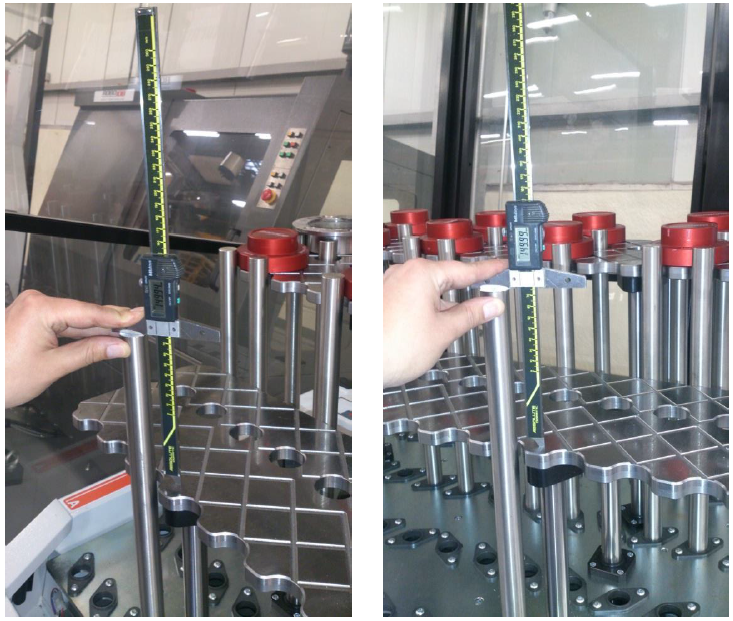
Adjust the height of the support bars until the table is parallel with top plate of the stacker.The difference in table height between the measurements (parallel error) should be less than 0,1 mm.
2.2. Navigate to the settings screen
Power on the stacker.Start the IPC and start the Multi-Assist software.Go to the configuration screen.
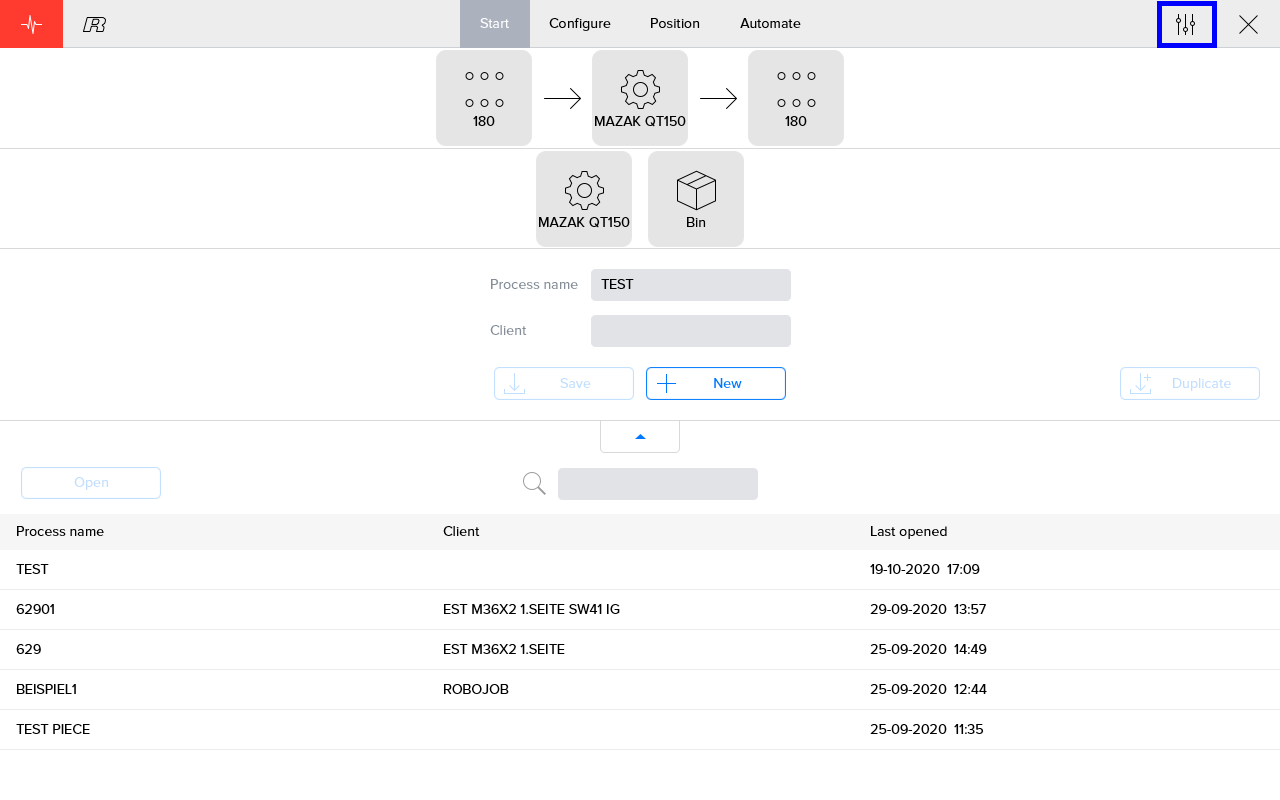
Log in with the password provided by RoboJob.
![]() |
Make sure to not change any other settings than the one shown in this document while the configuration is unlocked.It is not allowed to use the password for any other purpose than explained in this document. |

2.3. Calibrate the table
Navigate to the devices tab in the software.Select Servo-table and then Modbus.Choose the table to adjust.Motor 1 moves the front table, motor 2 the back table.
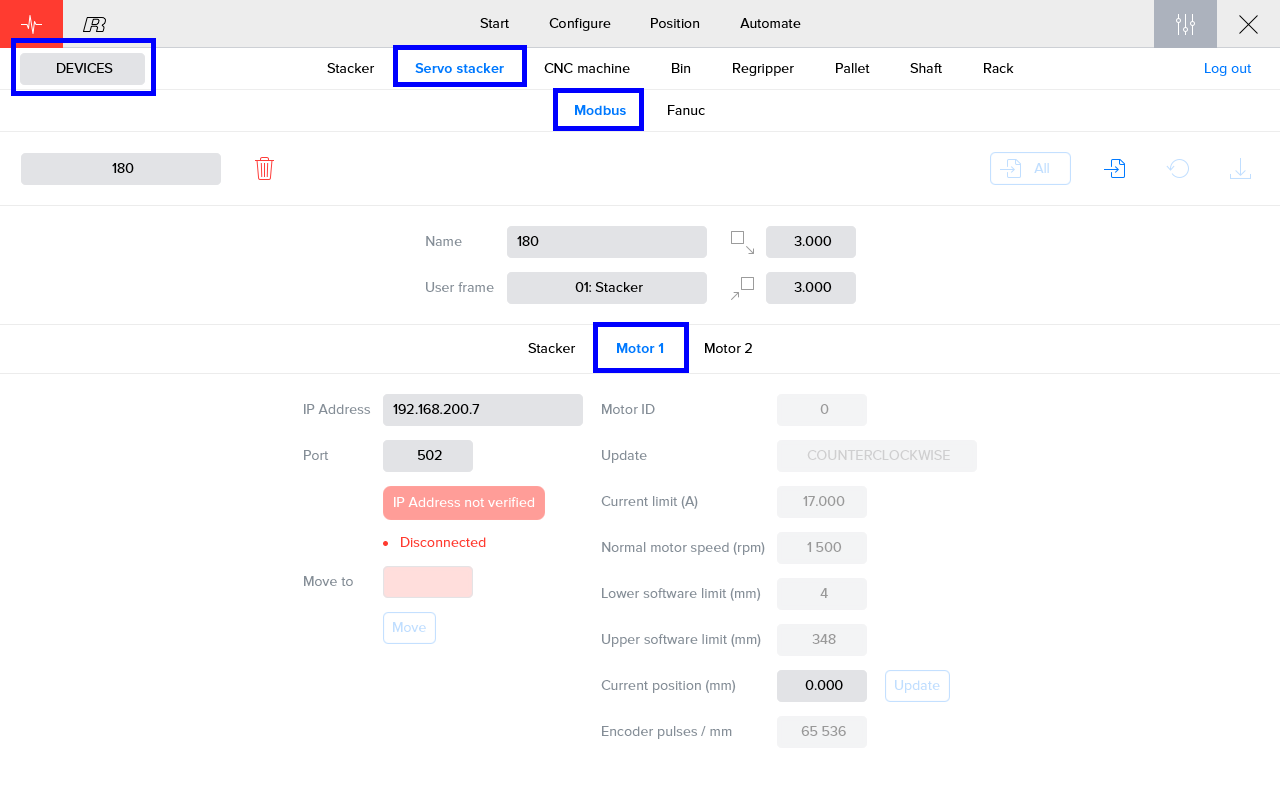
Enter the exact current table height which you have measured before.In this example the measured distance was 50 mm.
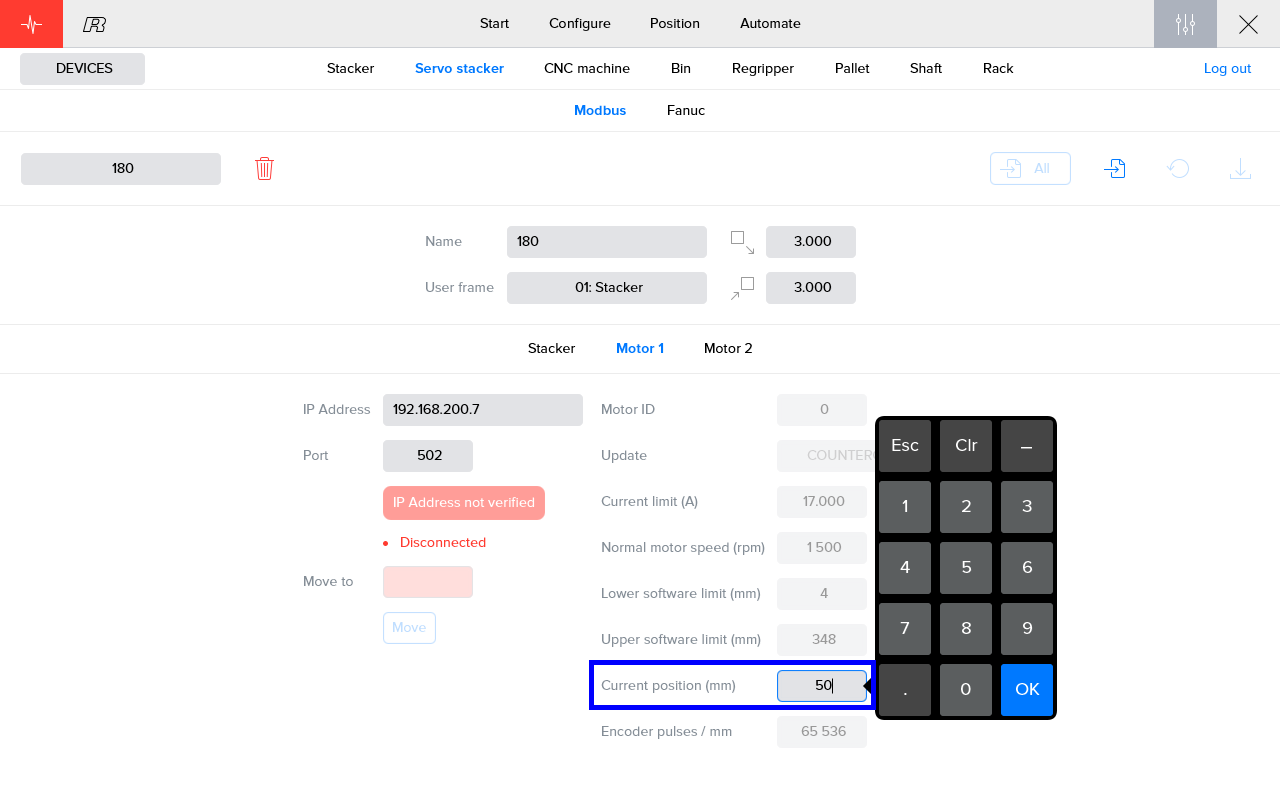
Send the adjusted value to the motor controller.
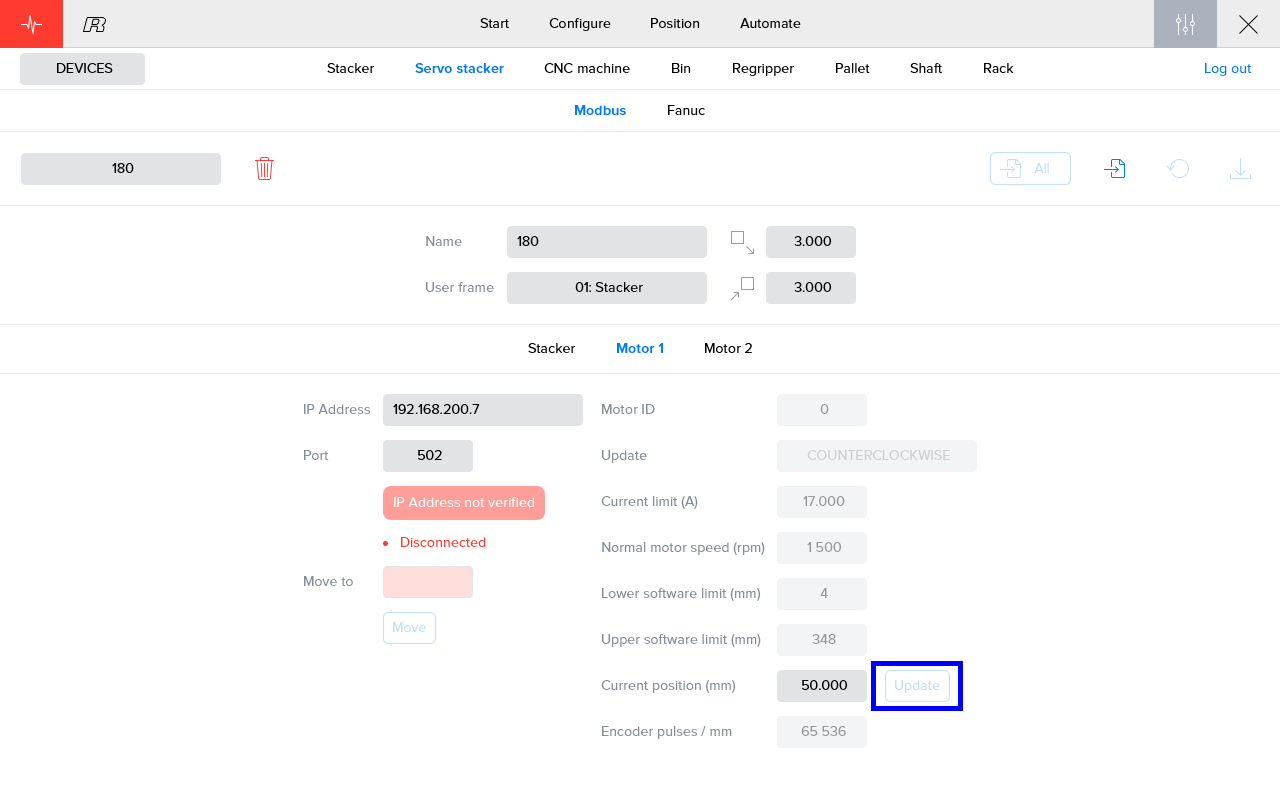
2.4. Restart the system
Shut down the system and wait for at least 30 seconds before powering back on.This will activate the new configuration in the motor controller.
3. How to get further help
Do not hesitate to contact us when you need additional support beyond the documents provided in the RoboJob Service Knowledge Base.
You may contact the RoboJob Service department using following means:
-
Help Center: service.robojob.eu
-
Email: service@robojob.eu
-
Phone: +32 15 70 89 70
We kindly ask you to provide us the following information:
-
Serial number xx-xx-xxx
-
Description of the fault or defective part
-
Exact error code or message
-
What did the robot do
-
What was the robot supposed to do
-
Pictures or videos
You can send this information to us via email.To send large files you may make use of a file transfer service like WeTransfer: robojob.wetransfer.com.
An automatic confirmation will be sent upon receipt of your mail.